Battery capacity can be recovered though reactivation of the lithium ions not contributing to battery charge and discharge, by combining battery diagnostics and electrochemical process
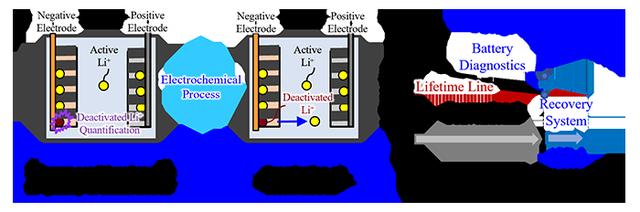
Fig 1: Capacity recovery technology for Lithium-Ion Batteries using an electrochemical process
(a) Internal battery diagnostics and Lithium Ion (Li+) reactivation;
(b) Extension of service life by recovering storage capacity
Hitachi has developed capacity recovery technology to extend the service life of Lithium-Ion Batteries (LIBs) built into power storage systems in a non-destructive manner. This innovation promotes a shift to mainly renewable energy power sources for power systems and a transition to electric mobility. The capacity of LIB is decreased during repetitive long-term charging and discharging, and then, battery replacement is necessary when the performance of battery system does not meet the requirement of a battery owner. This novel capacity recovery technology quantitatively evaluates the quantity of deactivated lithium ions (Li+) *1 that do not contribute to the charge and discharge in a non-destructive manner, and then reactivates the deactivated lithium ions through an electrochemical process executed according to specific conditions determined by a new analysis program. In an LIB cell*2 using conventional materials, we have verified this technology extends the LIB service life 20% by recovering 5% of the storage capacity when it falls below 80% of the initial capacity*3. Furthermore, we did not find any damage of the materials contained in the LIB after this electrochemical process. Hitachi aims to popularize highly efficient and sustainable power systems and contributes to the realization of a decarbonized society through the broad use of this technology by various operators from power transition and distribution to electric mobility businesses.
We plan to present some of the results of this research and development at the Hitachi European Innovation Forum on November 5, 2021 held in Glasgow, Scotland.
Future demand for LIBs is forecast to grow as stationary energy storage systems used for renewable energy and as power sources for electric vehicles. However, there is limited production and distribution of the rare metals used in batteries, which has the potential to tighten supply in the future. Moreover, LIB manufacture and disposal require a vast amount of energy. Therefore, suppressing performance degradation during use and extending the service life is critical to achieving a sustainable, recycle-oriented society. Initiatives to efficiently use LIBs while reusing these batteries for a wide range of applications are also essential. In light of these needs, Hitachi developed a basic technology to quantitatively evaluate a state of LIB degradation in a non-destructive manner and recover storage capacity in order to enable a longer service life (Fig. 1). The distinctive features of this novel technology are outlined below.
Technology details
1. Non-destructive, quantitative diagnostic technology of LIB degradation
The factors reducing LIB storage capacity are largely categorized as (A) degradation in positive electrodes, (B) degradation in negative electrodes, and (C) deactivation of lithium ions [Fig. 2 (a)]. Therein, Hitachi has focused on technologies to recover storage capacity by using an external electrochemical process to reactivate deactivated lithium ions. More specifically, a discharge in a range beyond the lower limit of battery voltage normally used temporarily increases the potential*4 of the negative electrode to extract the lithium ions not contributing to the charge and discharge in the negative electrode of the LIB. In order to determine a safe level of applied current preventing material damage, combustion, or other such hazards in the LIB during this process, the new technology quantitatively evaluates the state of degradation in the LIB in a non-destructive manner. In the Fig. 2 (b) indicating the relationship between the LIB storage capacity and voltage (hereinafter “capacity-voltage curve), we specifically focused on reducing the length of the capacity-voltage curve in conjunction with battery degradation. Through comparison of the capacity-voltage curves for the positive and negative electrodes measured and stored in a database in advance and the actual capacity-voltage curve of a degraded battery, we calculated the amount of lost capacity for each of the three factors described above. Of these three factors, we obtained the number of deactivated lithium ions in the electrolyte for (C) from the gap in the positions of the capacity-voltage curves for the positive and negative electrodes [Fig. 2 (b)], and then calculated a permissible level of applied current to safely reactivate lithium ions using this value and a unique analysis program.
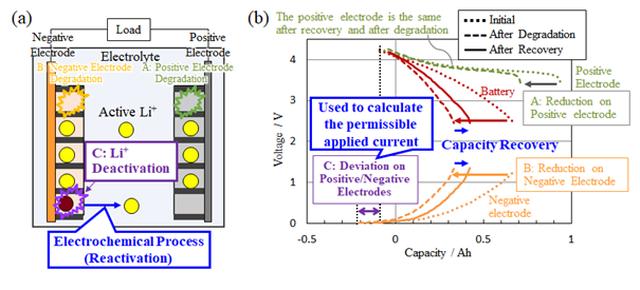
Fig. 2 Non-destructive, quantitative diagnostic technology of Lithium-Ion Battery degradation
(a) Factors lowering storage capacity;
(b) Changes in the storage capacity-voltage curves caused by each degradation factor and storage capacity recovery
2. Storage capacity recovery technology using pulse current control
The current concentrates around the external terminals of the electrodes and damages the material in that area as shown when the current is continuously applied, even if at the level calculated via the technology above. Therefore, Hitachi has leveraged its expertise accumulated in LIB control technologies to divide the applied current into pulse currents*5 of less than a few seconds. We discovered the method to ease the reaction for reactivating lithium ions using intervals of pulse current effectively prevents material degradation. As a result of optimizing various pulse current control conditions, we have verified an electrochemical process controlled using pulse currents recovers 5% of the storage capacity of an LIB cell using standard materials after a drop below 80% of the initial capacity due to repetitive charging and discharging and extends the service life by 20%. Disassembly to analyze the material structure and chemical composition of an LIB using this recovery method also confirmed no damage of the internal materials, even after the electrochemical process*6.
In the future, Hitachi will collaborate with customers who want to extend the service life of LIB storage systems in order to investigate the effectiveness of the capacity recovery when adapting this novel technology to storage systems used under a variety of conditions. Our aim is to extend the service life in customer system operations, reduce operational costs, enhance operation efficiency, save resources, and reduce energy consumption.
*1 Deactivated lithium ions refers to lithium ions which have changed to the lithium compounds or have been constrained in the negative electrode and no longer contribute to charge and discharge.
*2 Cell refers to the minimum working unit in a battery. The battery energy storage system with a larger capacity consists of numerous cells in parallel and/or serial connection. This research employed cells that use graphite in the negative electrode and lithium-nickel-cobalt-manganese oxide in the positive electrode.
*3 Service life refers to the lifespan until the LIB capacity drops below the capacity requirements of a power storage system. In this research, the capacity requirement as a remaining capacity which is 80% of the initial capacity is defined. A charge/discharge cycling test from 0%–100% at 50°C with a 1C-rate of charge and discharge proved the battery diagnostics and capacity recovery process extends the number of cycles by 20% until reaching 80% of the initial battery capacity. The 1C rate of charge and discharge is the current value to completely charge or discharge the battery capacity in one hour.
*4 Potential refers to the potential energy related to the amount of electricity (electrical charge) carried by particles or objects.
*5 Pulse current refers to an instantaneous current flowing over a short period of time.
*6 An X-ray diffraction analysis and Raman spectroscopy showed no damage in the crystalline structure of the positive and negative electrode materials before or after the capacity recovery process. In addition, inductively coupled plasma atomic emission spectrometry confirmed no elution of metal ions derived from the electrodes in the electrolyte solution after capacity recovery.
Battery lifecycle management video
Battery lifecycle management - Hitachi
www.youtube.comFor more information, use the enquiry form below to contact the Research & Development Group, Hitachi, Ltd. Please make sure to include the title of the article.
https://www8.hitachi.co.jp/inquiry/hitachi-ltd/hqrd/news/en/form.jsp