The “digital transformation” of factories is all the rage among manufacturers, but extracting useful data from the nexus of machinery and IT systems is often easier said than done. Integrating legacy infrastructure with software can be technically challenging, and seasoned machinists and IT experts often do not see eye-to-eye on how to innovate.
In this roundtable, Senior Director of Optimize to Grow at Hitachi Rail, Gianfranco Messina; Director of Marketing at Hitachi Digital Services, Shamik Mehta, and VP, Manager of the IoT Edge Lab at Hitachi America R&D, Sudhanshu Gaur address these challenges and more. Whether they are referring to manufacturing processes, the “digital maturity” of customers, or generative AI, their position is clear: the status quo is untenable: market, societal and even geopolitical forces are driving machinery — or "operational technology” (OT) in Hitachi’s parlance — and IT systems closer together. Their proposal — focus on outcomes, manageable projects, and close communication among stakeholders to build digitally enabled factories that change the way people work, as well as drive business growth.
Sudhanshu: Thanks, everyone, for coming together for this conversation. I’m looking forward to diving into our discussion on digital transformation, or DX, and smart factories. First off, could we define what we mean by “factory of the future,” “smart factory,” or “digital factory”?
Gianfranco: At Hitachi Rail, we envision smart factories to include four dimensions: process, technology, people, and sustainability. In our view, a smart factory must address all these areas. Our latest facility in Hagerstown, Maryland in the U.S. addresses all these requirements.
On the digital front, we are working with Hitachi America R&D and other Hitachi group companies such as GlobalLogic and Hitachi Digital Services to coordinate our entire technology stack and innovation efforts across an array of processes, from inventory and supply chain management to quality inspection and health and safety management, among others. The intelligence that we extract from these processes will, we believe, enable us to fundamentally transform the nature of factory work along with delivering bottom-line benefits.
In terms of people, the current generation is connected like never before. A factory that doesn’t enable digital workflows is a strange work environment for the new generation of factory workers. Usage of smartphones and tablets on the factory floor is a given. We need to implement solutions that make factories people-centric, as well as technologically innovative.
Lastly, there’s sustainability. Factories have a big impact on CO2 levels, so we must design with efficiency in mind. Smart factories need to be more than just digital factories. They need to be green factories. This is Hitachi’s vision. We believe it’s our social responsibility and we want to set an example for other companies.
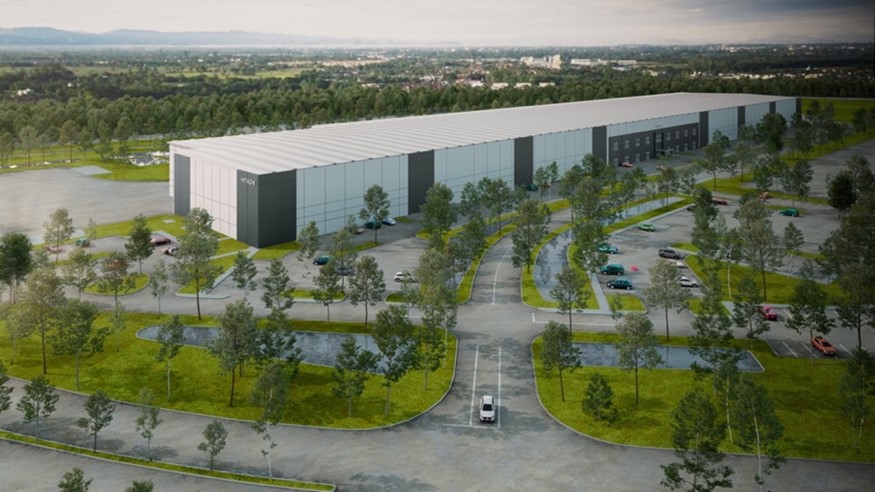
Hitachi Rail’s digital factory under construction in Hagerstown, Maryland, USA
Sudhanshu: My take is that the definition of “smart factory” has evolved over time. In the early 1900s, we had mass production. Now we are turning to more personalization and hyper-customization at scale. This shift is made possible by a highly elastic cloud, AI, robotics, 5G and other advanced technologies.
Gianfranco, your point about resilient supply chains is spot on. COVID disrupted supply chains globally. Currently, we are plagued by geopolitical instability. In addition, we face a shortage of skilled labor. How can you operate a factory in such uncertain times? Factories that aren’t equipped with the right tools and software to protect production from potential disruptions are just not viable.
Shamik: I see the emergence of smart factories as a cultural phenomenon involving the way companies and people think about manufacturing and work.
The U.S.A. manufactures 30 percent more products today than it did three decades ago, but with a fraction of the people. Expectations for productivity and profitability have changed dramatically. And, to your point Sudhanshu, expectations on customization and personalization have changed. But we’re working with one-fiftieth of the people we used to. This is happening in the U.S. as well as globally.
In short, human productivity is at an all-time high, enabled by more automation, more software, and more AI. We are doing more with less, of course, but we are also doing things differently.
So, investments in digital technologies will continue unabated. According to Gartner, 80 percent of CEOs in the manufacturing industry are increasing investments in digital technologies, led by AI, IoT, and data and analytics.*1 Innovations based on these technologies will manifest themselves on the factory floor like never before.
*1 Sources of Greenhouse Gas Emissions, EPA, United States Environmental Protection Agency,
https://www.gartner.com/en/industries/manufacturing-digital-transformation
Where art thou, customer?
Sudhanshu: I think we can all agree that the digital transformation of factories is essential, if not inevitable. But where do our customers stand? If you look at reports from industry analysts on the success rate of so-called DX initiatives involving smart manufacturing, the numbers, at under 10 percent, are extremely low.
When we talk about manufacturing, we’re working with predominantly legacy infrastructure. That makes it difficult to scale any digital solution from one production line to another, or any one factory to another. This has been a big challenge. How do we enable customers to integrate new tools into their factories?
Shamik: At Hitachi Digital Services, we find that our customers occupy four different areas in the “digital maturity model.”
Some customers are extremely sophisticated, using sensors to capture and digitize information on digital “gemba,” or factory floor, boards. This information is collected and shared by production leaders within the company, and in some cases around the world, to gain visibility into production runs.
Some customers have signed up with vendors, including Hitachi, who can help them create digital twins for their assets.
On the other end of the digital maturity model, people are writing down their observations on sticky notes placed on whiteboards inside the management room above the factory floor, things like what knobs were set to where, or how many times did the machine break down, rattle too much, or get hot?
Some customers are just now beginning to investigate basic data integration tools. This gets complicated because their existing assets are old-they were built before the Internet, and they’re not connected.
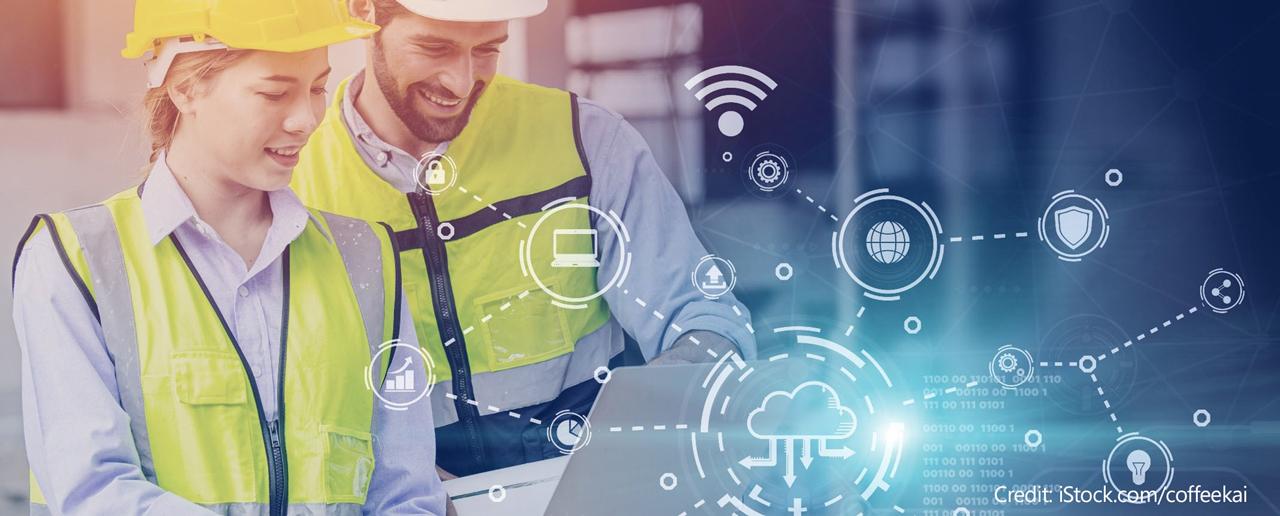
The OT x IT challenge
Sudhanshu: I’m with you, Shamik. Drawing from my experience working with auto parts manufacturer Hitachi Astemo, which has over 130 manufacturing sites spread across more than 25 countries, there’s a great deal of variation in digital maturity. They are at various stages of the technology adoption lifecycle.
Also, I think we need to make a more nuanced distinction as to whom we mean by “customer.” With manufacturers, there's the IT division, which is more eager to bring digital technologies into the organization to help the production team. But the production team, which has been using the same set of tools and technologies for the last 40 years, would rather avoid any friction created by new tools being introduced to the shop floor.
When we talk about smart manufacturing, it’s at the cusp of these two different roles, the IT part and the machinery or production part, what we at Hitachi call “operational technology,” or OT.
Sometimes the production teams doubt that they will benefit from the latest IT tools. There can be a complete lack of awareness of the benefits of IT, although this is changing with the advent of technologies such as the metaverse that allow manufacturers to model and visualize the benefits of their investments.
At auto parts manufacturer Astemo, they were among the few global automotive players who used the cloud to orchestrate and manage production data. The cloud offers scalability and ease of integration. You don’t have to worry about managing or maintaining the infrastructure and it’s pay-as-you-go, which is crucial for early trials where ROI may not be immediately verifiable. We are only now beginning to see the benefits. Astemo is well-prepared now, with readily accessible data and cloud infrastructure which connects their factories globally. That makes it possible to bring in any emerging digital solution or technology without investing too heavily in additional capital up front.
Shamik: We’re seeing many customers struggle with merging OT and IT data. If you want to make something like a ChatGPT model work, it can’t work with just IT data. It must understand operational data. You need to figure out trends, apply a model, and correlate it with higher-level processes, like a supply order, customer demand, pricing information, or requests for customization, which are of course information technology data sets.
Operational data is where you have an asset performance model, a digital twin, or a model that helps you measure the quality or performance throughputs of equipment. Operational technology and the data sets, formats, locations, places and tools that store and manage it are very different from informational enterprise data sets such as customer relationship tools, sales outlook, production demands, and other business planning software.
For a company to truly benefit from OT and IT integration, they cannot just blend the data. Rather, they need to understand what data is useful, drop what’s not, and figure out a way to contextualize and normalize the data so it’s usable by multiple personas, based on their needs. They need to start with the business process. That way, you can draw insights out of holistic, merged IT and OT contextualized data.
Empowering the factory floor: DX at Hitachi Rail
Gianfranco: I’ve spent the last thirty years working on transformation projects. “Smart factory” essentially means innovation in manufacturing, and we have two types of innovation: step-by-step, or continuous improvement, on one hand and radical innovation on the other.
IT and OT enable continuous improvement by integrating business processes with new tools and features. Where we see the most advancement on the factory floor is in the support function, which includes improving quality checks, logistics, and testing.
At our factory in Maryland, we look to improve efficiency and quality, and we are experimenting with new technologies to improve training and collaboration. We see the cloud enabling us to scale quickly, though we are of course cautious about cybersecurity.
We recently tested a truly transformative solution with Hitachi America R&D that combines Hitachi’s AI models and a robotic dog, running on industrial 5G. The solution enables quality control inspectors to examine factory operations and products to ensure they meet essential quality and safety standards. It integrates seamlessly with other factory systems including manufacturing execution systems (MES), providing an integrated experience of automated quality inspection triggered by events on the factory floor. We believe the productivity gains from this solution will be remarkable. The worker experience will be transformed as well.
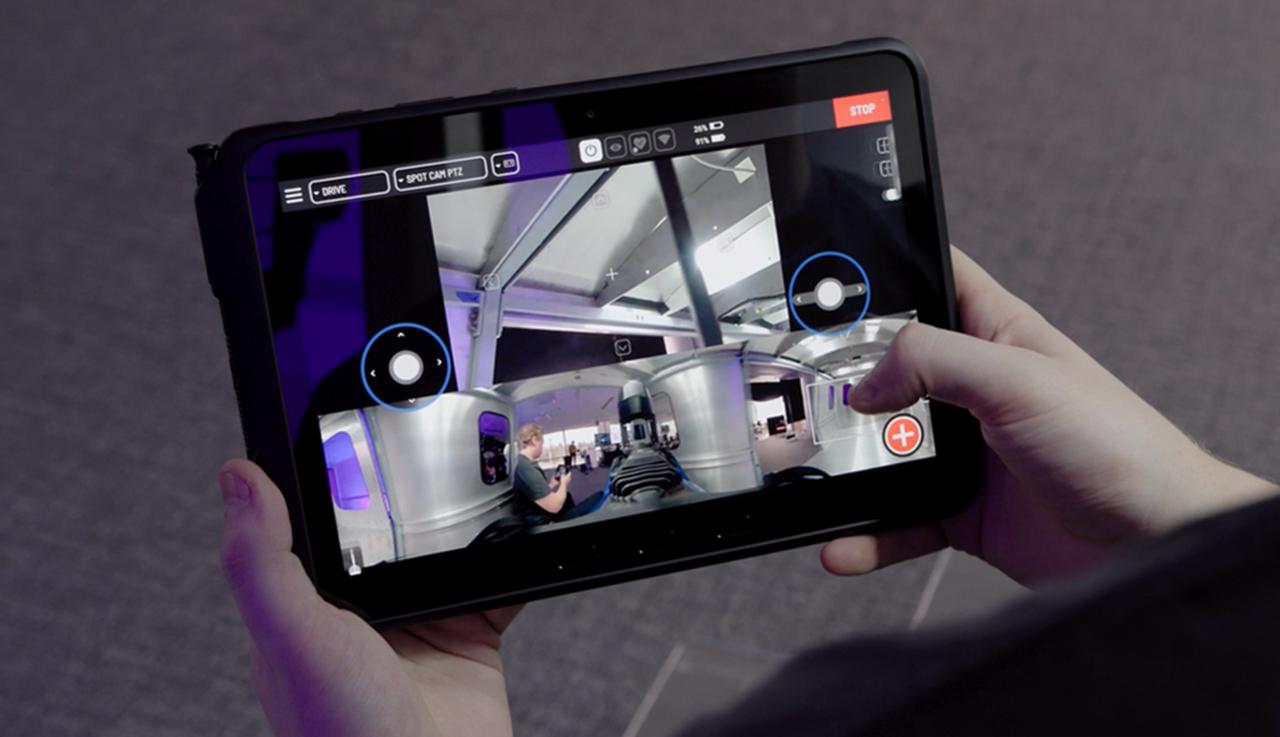
Sudhanshu and his team are also centralizing management of the data that we gather from such solutions, along with data from our supply chain and health and safety initiatives, in a unified data layer. The longer-term plan is to make this platform available to customers.
Sudhanshu: As mentioned, between the labor shortage, trade wars, and uncertainty in the supply chain, companies want to have their suppliers closer to home. And the Maryland factory is a great showcase for that.
Gianfranco: Indeed, it is. We can also invite Hitachi Digital Services’ customers to demonstrate what we’re able to do, promoting onshore manufacturing to other manufacturers.
Before and after generative AI
Sudhanshu: I’m certain that solutions like quality inspection combining AI and robotics will become mainstream. Additionally, generative AI now enables workers to interact with technology using natural language, creating a seamless interface between technology and the workforce. Furthermore, since these solutions are multilingual, they offer significant benefits to companies operating factories worldwide.
But of course, the impact of generative AI extends way beyond language recognition. Generative AI is triggering a major shift in how people think about technology and work. There’s a before and after scenario at play, with generative AI playing a huge role in areas such as maintenance, quality inspection, and customer service, among others. The mindset of manufacturers is changing in terms of how they may be able to benefit from advanced digital tools and technologies.
Also, as mentioned, with generative AI, combined with augmented reality (AR) and the metaverse, we can now unlock new levels of flexibility and interactivity in modeling and visualizing solutions. The technology is highly accessible to end users, enabling them to actively engage with, imagine and visualize their future operations. This is an enormous benefit.
Natural language processing can bridge the gap between your application and the unstructured data that lies behind it. You can finally glean insights from the data without building dedicated software solutions. Generative AI can foster greater innovation and adaptability, whether it’s for predictive maintenance, production efficiency, or addressing the labor gap in the market.
Visualize a vast ocean, but start with a bottle of water:
Bringing smart factories to life
Sudhanshu: In closing, what advice would you give customers who are looking to modernize their factories leveraging digital solutions and advanced technologies?
Shamik: My advice is simple: ask why. Why are you pursuing digital transformation? What is your business case? What outcomes do you want to realize? Are you focused on the top line or bottom line, or both?
You need to make your intentions very clear from the start and have all stakeholders agree on them. Your OT and IT teams need to be working together. If they’re not, it’s most likely because the business impact of making a joint vision has never been agreed upon, let alone discussed.
To your point, Sudhanshu, production teams often resist the adoption of new technologies. But without their buy-in, a DX initiative will go nowhere. I recently met with a customer that abandoned their scheduling optimization project after four months because they realized they didn’t need it.
You can capture tons of data from “man, machine, materials and methods,” but what is it for? Why invest time on and pay for extracting and storing all this data if you can’t visualize its business impact?
Again, from an implementation standpoint, you need to start with the process that you are looking to digitize-whether it’s scheduling optimization, quality inspection, or inventory management-and work backwards. This way you can identify the OT and IT data that you need and be more efficient as well as impactful.
Sudhanshu: I think the way to navigate the complex labyrinth of OT and IT integration is, for one, to involve important stakeholders from both the OT and IT teams in the solution design from the outset. Early alignment is essential. [](sudhanshu:)
Second, once you've got the integration to work, to replicate the solution across multiple deployments without too much customization, it's beneficial to conduct a thorough analysis of the variability across manufacturing lines, including users, and to design an architecture accordingly, while also aligning with the company's IT policies for a smoother rollout.
Finally, considering the financial impact on the customer, particularly around operational expenses, and the total cost of ownership, is of course mandatory as well. Careful planning of capital investments and a sharp focus on ROI estimation are indispensable, especially when the technical aspects of the digital solution have been well-addressed.
Gianfranco: I want to give you a metaphor about digital transformation. A customer should think of a beautiful ocean, say, the Caribbean. But their thoughts should start from a small bottle of water. That bottle of water could become a bucket, a small lake, then a big one, and then the ocean.
In other words: Think big and think better but act small. And escalate fast.
Find a partner who can help you advance quickly because time is of the essence. If you take two years to understand the return on investment for a project, that’s too long. How could you explain the return on investment for the Caribbean Sea? But you can easily explain the return on investment of a bottle of water.
My last piece of advice is about people. Choosing the right people to engage on a project is key. Digital advancement means co-creation. You can’t only act internally. That would only lead to incremental progress. You need someone with domain expertise, who’s passionate about technology, to break all the paradigms, and reshape and redesign the process from the outside in. You need the right mix of passion and resilience.
Sudhanshu: That’s a great note to end on. Thanks, everyone, for participating today and sharing your valuable insights with us.
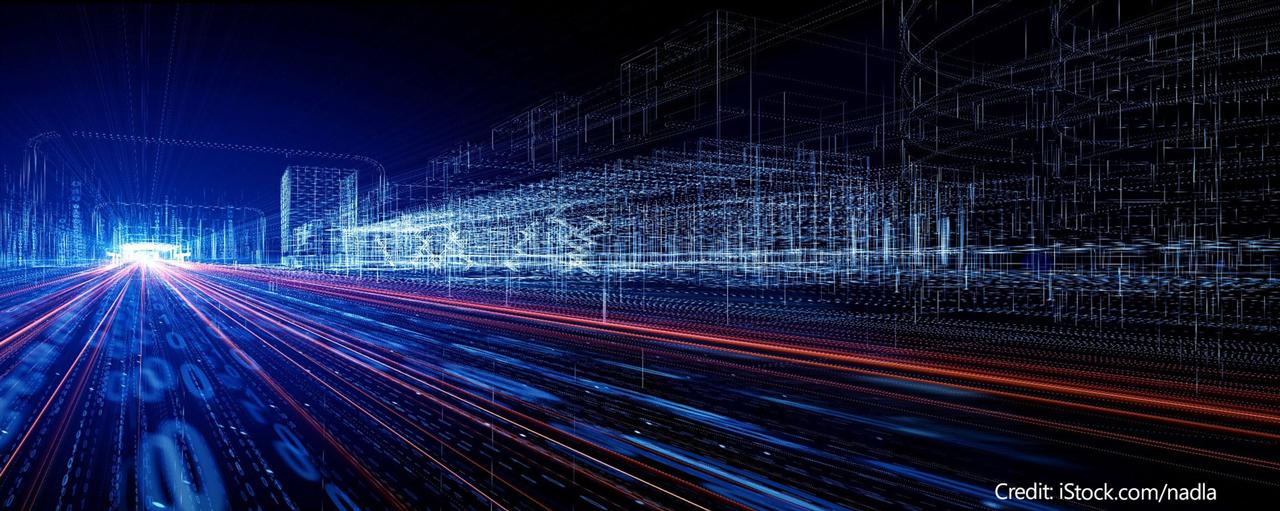
The digital transformation of factories is not just about integrating hardware and software. It’s about merging different mindsets and work styles. Working with machinery is very different from operating software and managing data. Bridging these functions requires strategic thinking and a commitment to outcomes. Knowledge of the latest technologies, from generative AI and the metaverse to robotics and 5G, is of course mandatory. But strong communication skills, if not diplomatic talent, are also essential. Enlisting partners with deep manufacturing and IT expertise can also bring clarity and focus to a factory’s DX journey. At the end of the day, digital transformation is about welcoming change and collaboration.
(This discussion has been edited for clarity.)
Profiles
(As at the time of publication)
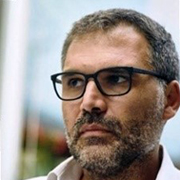
Gianfranco MESSINA
Senior Director, Optimize to Grow
Hitachi Rail Ltd.
Gianfranco Messina has more than 20 years of experience in business transformation projects that integrate operational technology and IT to achieve maximum operational efficiency and cost reduction. He has led complex, global, multi-site projects in the aerospace, information technology, oil and gas, and railway industries.
Currently, Gianfranco is leading smart factory lighthouse projects for Hitachi Rail in Italy and in the United States. For Hitachi Rail’s current project in Hagerstown, Maryland in the U.S., Gianfranco’s team is aiming to build one of the most advanced digital factories in the world whose innovations can be shared with Hitachi’s manufacturing customers worldwide.
Gianfranco has a master’s degree in business process reengineering.
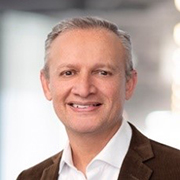
Shamik MEHTA
Director, Marketing
Hitachi Digital Services, LLC
Shamik Mehta is the director of marketing for cloud and application modernization services at Hitachi Digital Services. He has 25 years of experience in product and strategic marketing and applications in data management and data analytics software, industrial IoT, semiconductors, renewable energy, and e-mobility solutions. He has held roles in product marketing, product management, operations and technical sales for complex technology products, including software services, solutions and data platforms for banking, financial services, and industrial applications.
Shamik has experience managing global product marketing, GTM activities, thought leadership content creation and sales enablement activities for technology and software applications for Banking and Financial Services, Manufacturing, Energy, and Transportation verticals. Shamik is a Silicon Valley native, having lived, studied and worked there since the early 90’s.
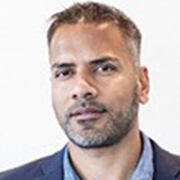
Sudhanshu GAUR, PhD
Vice President and Manager of the IoT Edge Laboratory
Research & Development Division
Hitachi America, Ltd.
Sudhanshu Gaur leads the edge computing R&D program, nurturing innovative solutions across diverse technologies including 5G, robotics, computer vision, and generative AI applications. His role extends beyond the R&D organization, helping to shape the Industry 4.0 vision for digital transformation across key players like auto parts manufacturer Hitachi Astemo and Hitachi Rail. Currently, Sudhanshu is leading the entire IT x OT orchestration, including partner ecosystem development, to enable the lighthouse vision for Hitachi Rail’s new factory in Hagerstown, Maryland, USA. Previously, Sudhanshu served as Chief Architect of Smart Manufacturing at Astemo, where he was responsible for driving the Industry 4.0 initiative across more than 140 manufacturing sites globally.
Sudhanshu was named among the top 25 leaders transforming manufacturing by the Society of Manufacturing Engineers (SME) in 2020. Before joining Hitachi, he received his Ph.D. degree in Electrical & Computer Engineering from the Georgia Institute of Technology, and Master’s and Bachelor of Science degrees from Virginia Tech and the Indian Institute of Technology, Kharagpur, respectively.