Achieves Accurate Positioning Control at Low Cost by a Crawler-type Driving Mechanism with High Road-handling Ability even on Unpaved Roads
Hitachi has developed an autonomous-mobile robot that combines technology for recording the positions of peripheral objects and generating a map while driving and technology for achieving high positioning accuracy both indoors and outdoors by a crawler-type driving mechanism *1 with high road-handling ability. This robot can be used to perform inspection work in place of human labor when sending people to the field is difficult due to a remote location, the occurrence of a disaster, or the effects of a pandemic, staff shortage, etc. When applying this robot to the inspection of infrastructure facilities, Hitachi estimates that the work previously done by people can be reduced by about 75% in a model case.
Hitachi introduced this robot to the world in the video “Hitachi’s Omika Works: The First Japanese Company to be Elected “Lighthouse” by the World Economic Forum (WEF)” presented at the Hitachi Social Innovation Forum held in November 2020 *2.
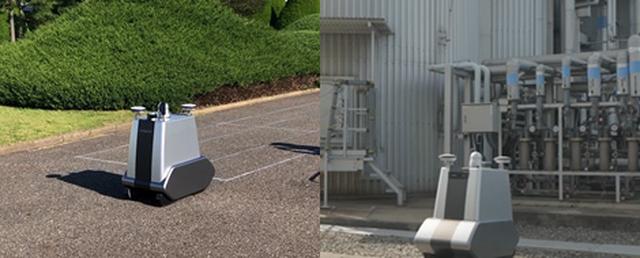
Fig. 1. Hitachi-developed crawler-type autonomous-mobile robot
Background and issues
- The work of inspecting aging infrastructure facilities is not going well due to the aging of workers and shortage of qualified personnel brought on by the declining birthrate and aging population in Japan.
- With the spread of COVID-19, the need is growing for inspecting facilities without traveling to the target site such as by remote work.
- To enable robots to perform inspections either indoors or outdoors even on unpaved roads or paths having an uneven surface, there is a need for technology that can control driving through stable and highly accurate positioning.
Developed technology
- Technology for generating maps and estimating own position for use in low-cost autonomous driving
- Control technology for achieving high positioning accuracy indoors or outdoors for a crawler-type driving mechanism
Details of developed technology
1. Technology for generating maps and estimating own position for use in low-cost autonomous driving
Performing robot-based inspections requires a map recording the autonomous driving route and technology for estimating the robot’s position on the map. Maps commonly used in self-driving vehicles are costly since they are generated using vehicles equipped with specialized high-accuracy sensors. Hitachi already had technology that enables a robot to generate a map on its own by recording information on the area and route driven, so we developed technology for applying that technology to inspection robots to generate a map of the indoor/outdoor inspection route without additional cost and to estimate the robot’s own position. Specifically, Hitachi developed a method that statistically matches the features of obstacles recorded on a previously generated inspection-route map with the features of obstacles on a map generated using the peripheral information and driving path obtained during actual inspection driving from sensors mounted on the robot. This method made it possible to follow the inspection route at low cost.

Fig. 2. Technology for generating maps and estimating own position in autonomous driving.
2. Control technology for achieving high positioning accuracy indoors or outdoors for a crawler-type driving mechanism
Autonomous driving based on a map requires accurate understanding of position on the map and driving with high positioning accuracy along the route on the map according to the understood position. Self-driving vehicles generally use GNSS *3 or LiDAR *4 sensors to determine position on a map, but GNSS cannot be used in places out of reach of radio signals or indoors while LiDAR cannot be used if no characteristic objects (landmarks) exist in the surrounding area. In addition, the robot presented here adopts a crawler-type driving mechanism having high road-handling ability even on unpaved roads, but with this type of mechanism, positioning errors can occur due to transfer lag between the drive wheel and crawler belt, slipping on the ground, etc. As a result, it has been difficult up to now to increase positioning accuracy while driving. Against this background, Hitachi developed (1) technology for estimating the robot’s own position on an indoor or outdoor inspection route by combining GNSS and LiDAR and (2) driving control technology to enable the robot to follow the indoor or outdoor inspection route based on position offset *5 from the inspection route. Hitachi also developed feedforward and feedback control technology to compensate for transfer lag between the drive wheel and crawler belt or for slipping on the ground. On measuring error between the target and actual driving locus on a model driving route after installing these control technologies, it was confirmed that autonomous driving could be performed with error under 3.5 cm. This error figure corresponds to a high level of accuracy approximately one-fifth that of the control method for conventional crawler-type driving mechanisms.
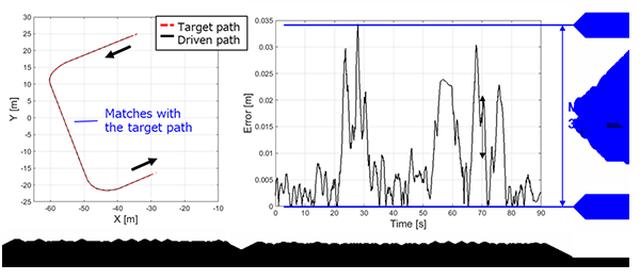
Fig. 3. Achieving high positioning accuracy indoors or outdoors for a crawler-type driving mechanism.
*1 Crawler-type driving mechanism: A driving mechanism equipped with a crawler belt that covers a drive wheel, road wheels, and idler wheel. Since drive power is transferred in the order of drive wheel → crawler belt → ground, power transmission loss is high, and in the case of an uneven surface, the contact area between the crawler belt and ground decreases making it easy for slipping to occur. For these reasons, positioning control during driving has been difficult in conventional control methods.
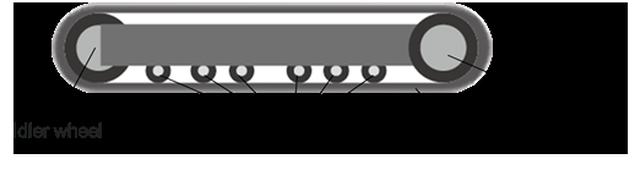
Fig. 4. Crawler-type driving mechanism
*2 URL of video introduced at the Hitachi Social Innovation Forum: https://www.youtube.com/watch?v=DgVJAfBIVfs
*3 GNSS: Global Navigation Satellite System
*4 LiDAR (Light Detection and Ranging, Laser Imaging Detection and Ranging): A sensor-based method for measuring distances to objects using laser irradiation.
*5 Position offset (lateral deviation) from the travel route on the axis orthogonal to the travel route at a waypoint specified on the map.
For more information, use the enquiry form below to contact the Research & Development Group, Hitachi, Ltd. Please make sure to include the title of the article.
https://www8.hitachi.co.jp/inquiry/hitachi-ltd/hqrd/news/en/form.jsp