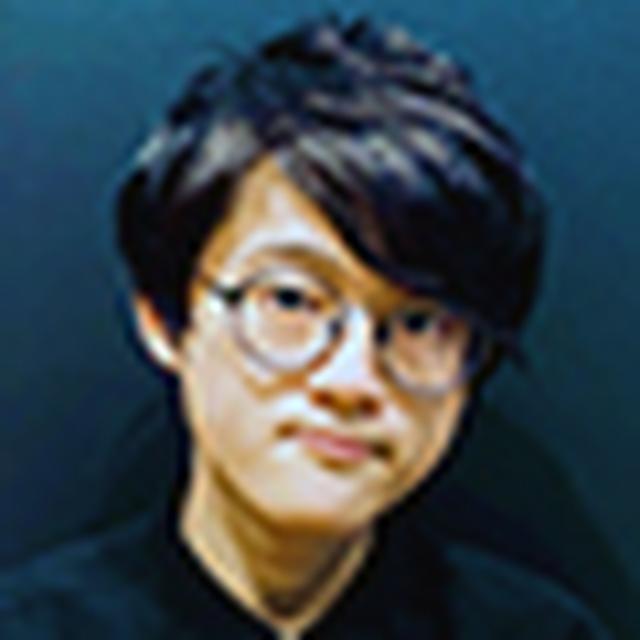
Daisuke Yagi
Research & Development Group, Hitachi, Ltd.
According to Statista, humans produce nearly 300 million metric tons of plastic waste each year*1 and according to a prediction model announced by the University of Leeds, if this waste is not properly managed, then there will be 1.3 billion tons of plastic waste in the environment by 2040.*2 That’s a lot of plastic, and plastic wasted.
Plastics as a material has many benefits but as waste, it is a global challenge that requires a holistic approach if we are to realize a sustainable society within planetary boundaries. And, according to the OECD, less that 10% of plastics used around the world is being recycled. *3 So what can we do to facilitate the re-use/recycling of plastics; make the most out of what we have, and to reduce our need for virgin plastics and our dependence on this fossil-fuel based material.
My colleagues and I have been looking at how we can improve the quality of recycled plastics. Most of the plastics around us are manufactured using what we call an injection molding process. In the injection molding process, an injection molding machine is used to melt raw materials, called pellets, which are then injected into a mold and allowed to cool and solidify to produce plastic.
The material properties of recycled pellets which are made from waste plastics, however, tend to fluctuate between production lots due to various contaminants and other factors throughout the recycling process (Fig.1). Therefore, when molding plastics with recycled pellets, the quality of the recycled material is not consistent.
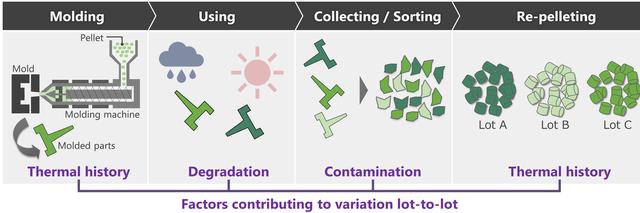
Figure 1. Example of factors that fluctuate material properties in the recycling process
To use recycled materials with material properties that fluctuate from lot-to-lot, conventionally, a skilled operator made fine manual adjustments to the injection molding process conditions according to the material properties. As this is time consuming and requires experience, this has limited the type and amount of recycled materials used as manufacturers have sought to use recycled materials with consistent properties.
To address this issue, my colleagues and I conducted a study where we looked at how we could automatically optimize the process conditions and thereby contribute to quality, and presented our results at the 37th International Conference of the Polymer Processing Society (PPS-37) which was held in Fukuoka, Japan, from 11-15 April 2022.*4 Below, I’d like to briefly share what we did.
So how did we optimize the process conditions?
In a nutshell, we installed sensors inside the molds to measure fluctuations in the properties of the recycled material and then analyzed the sensing data using machine learning. Let me explain more about the technology developed and examples of its application.
Optimization of process conditions is performed in the following three steps. The first step is to create a training database (Training DB) that links process conditions, molded parts quality, and recycled material properties.
In this study we used “weight” which is often used as a quality control indicator in production for the quality of the molded parts. The Training DB was constructed by combining the process database (Process DB) and the feature database (Feature DB) (Fig.2).
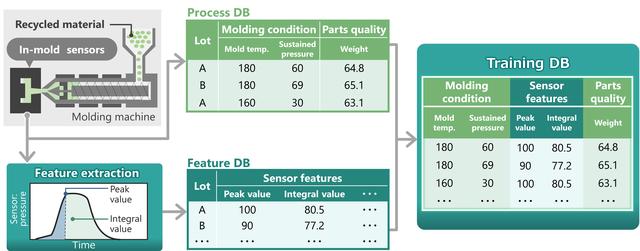
Figure 2. Conceptual diagram of configuring the training database
Based on the Design of Experiment, data linking the recycled material lot, process conditions, the weight of molded parts accumulated while changing the process conditions and recycled material lots, were accumulated in the Process DB.
The Feature DB accumulated data correlating the sensor features to the properties of the recycled materials by material lot. The sensor features were extracted by molding each lot of recycled materials under standard process conditions common among lots and analyzing the sensing data from various in-mold sensors, such as pressure sensors.
Next, a regression model was constructed from the training data accumulated in the Training database, with the process conditions and sensor features as explanatory variables and the weight of the molded parts as the objective variable. To streamline the process of building regression models, in this study, we generated highly accurate regression models by automatically selecting the best algorithm from multiple machine learning algorithms.
Finally, we obtained the sensor features by molding the lot to be optimized under the standard conditions. Using the sensor features and the constructed regression model, we then extracted the optimized process conditions using inverse analysis. The procedure for the inverse analysis in this study is shown below in Figure 3.
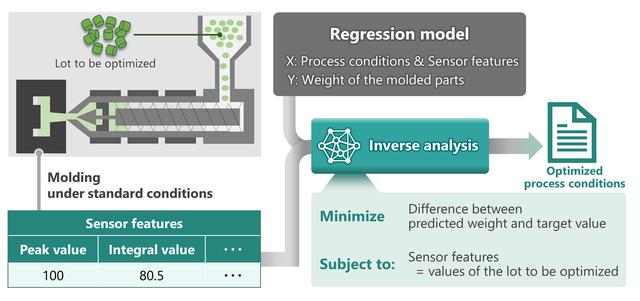
Figure 3. Conceptual diagram of optimization of process conditions by inverse analysis
First, we set multiple candidates for each explanatory variable and created all combinations of them. Then, by inputting the combinations into the constructed regression model, we predicted the weight of molded parts corresponding to each explanatory variable. Lastly, the combination of explanatory variables closest to the target value among the predicted weight, was selected as the best explanatory variables. Here, as a restraint condition, the sensor features in the explanatory values were fixed at the values of the lot to be optimized in order to obtain process conditions that are individually optimized for the lot.
What were the results?
When we applied the technology developed to five lots of recycled polypropylene material, the weight of the molded parts molded under the optimized process conditions approached the target value in all lots (Fig.4). The results indicated that lot-to-lot variation in molded parts weight was reduced, and that greater stability in molded parts quality was achieved.
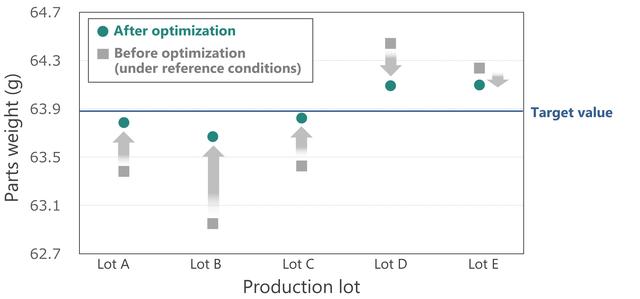
Figure 4. Reduction in weight variations between molded parts as a result of optimizing molding process conditions for each recycled material lot
What’s next?
In this study, we developed a technology to automatically optimize injection molding process conditions and found that it stabilized the quality of molded parts by controlling the molding process using in-mold sensor data, even with varying recycled material properties between production lots. As a next step, we plan to apply this technology to a wider range of recycled materials with the aim of contributing to a circular economy through the reduction of plastic waste.
Reference
*1 Statista: Annual production of plastics worldwide from 1950 to 2020.
*2 Phys.Org – News: A world drowning in plastic pollution by University of Leeds, 23 July 2020
*3 OECD: Plastic pollution is growing relentlessly as waste management and recycling fall short, says OECD, February 2022
*4 D. Yagi, H. Nakatsuchi, R. Shimada and K. Kobayashi. “Injection molding process optimization for stabilizing parts quality of recycled materials by using in-mold sensors,” presented in Oral Session #G01-43 of the 37th International Conference of the Polymer Processing Society (PPS-37), 12 April 2022, Fukuoka, Japan.