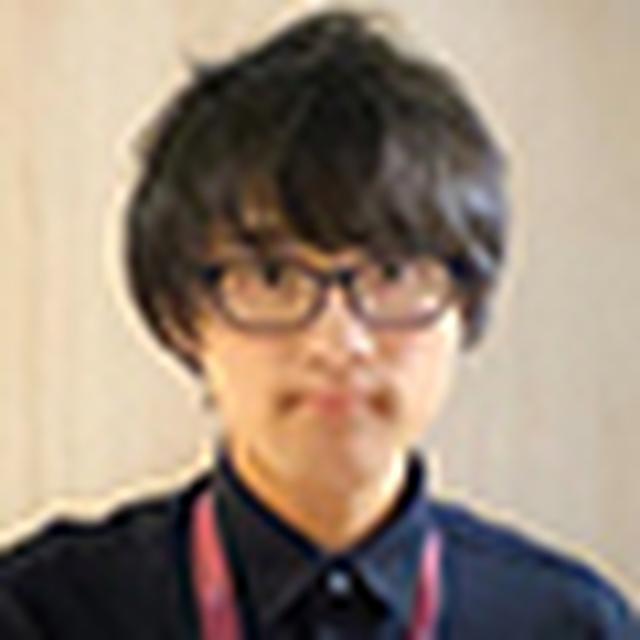
Daisuke Yagi
Research & Development Group, Hitachi, Ltd.
Background
In the manufacturing industry, production methods can be categorized into two types: discrete manufacturing and process manufacturing. Discrete manufacturing creates products through mechanical processes and assemblies, e.g., automobiles. On the other hand, with process manufacturing, the reactions between gas or liquid materials and ingredients create products, e.g. chemicals. The ability to visualize what is happening in process manufacturing is falls short of discrete manufacturing as it is a composite and continuous process taking place in plants or pipes. Thus, when a defect is generated, operators often need to go through a process of trial and error to identify an effective countermeasure because it is difficult to discriminate the factors contributing to the defect. As a result, when there is a defect there is often a long production downtime while countermeasures are being sought. To address this issue, we developed an operation recommender system that automatically discriminates the factors contributing to the defect and determines the appropriate countermeasures using data from sensors installed in the production line together with past countermeasure records.
To explain how the operation recommender system works, let’s take as an example, the highly functional film production process. Figure 1 is a conceptual diagram showing how the production process is composite and continuous until inspection.
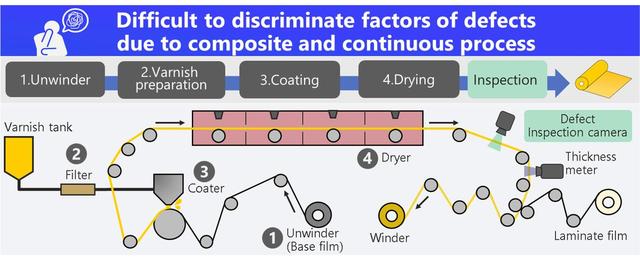
Figure 1: Conceptual diagram of a production line. First, the base film is transported and the varnish is prepared. Next, the varnish is coated on the base film, and the solvent is dried in a dryer. Inspection takes place at the end.
How the operation recommender system works
Figure 2 shows an overview of the system. Firstly, the countermeasures implemented in the production line are linked with factors of defects extracted by fault tree analysis (FTA) in advance. Secondly, various sensors related to the factors are selected. Thirdly, the relationship among their data is modeled by Gaussian process regressor (GPR) which is one of machine learning methods. Here, the normal state data where no defects are generated is used as training data. Finally, anomaly scores (ASs) of factors are calculated during manufacturing, then the factor with the highest AS and the countermeasure can be determined.
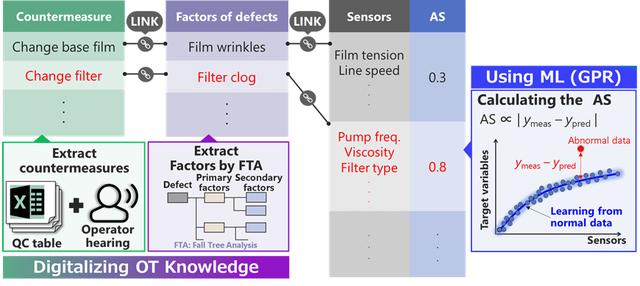
Figure 2: Overview of the developed system. The system has two developed factors: the digitalizing Operation Technology (OT) knowledge and the calculation of AS by using GPR
In order to compare between the factors, the AS is normalized in consideration of the probability density function of the AS for each factor. Because the factors are corresponding to the countermeasures, as shown in Figure 3, the developed system prioritizes and recommends countermeasures to workers to support their decision-making.
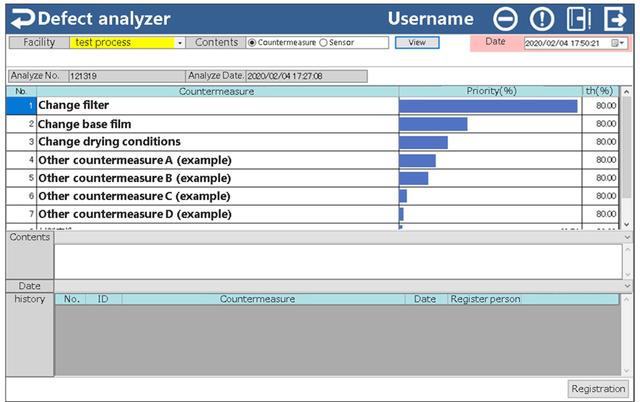
Figure 3: Sample GUI of the developed system. When defects are generated, operators launch it.
Operation recommender system example use case
Figure 4 shows an example of verification of the developed system: an AS chart for each factor. When defects were generated, “Film wrinkles” was the highest AS in all factors and the countermeasure predicted by the developed system was “Change base film”. After “Change base film”, no defects were generated, and the AS decreased to the same level with other factors. Thus, the predicted countermeasure was consistent with the implemented one. As a result of this verification by using actual process data, which is not training data, it was confirmed that the accuracy of the predicted countermeasure was higher than 90%.
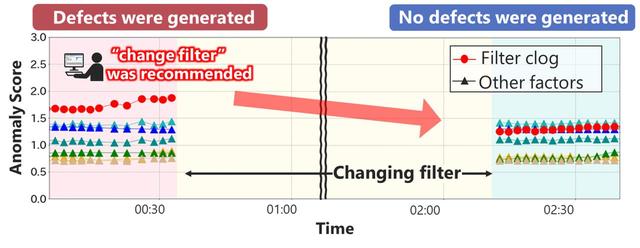
Figure 4: Example of verification. No defects were generated by the predicted countermeasure.
Conclusion
To contribute to resilient manufacturing systems through digitalization, it will be important to connect physical phenomena, OT knowledge and sensor data in parallel with developing AI to analyze and learn from the data. My colleagues and I developed an operation recommender system that can discriminate factors contributing to defects and recommend appropriate countermeasures. We will continue developing the technology to resolve issues in manufacturing by considering different manufacturing processes.
This work was presented at the 2020 Annual Meeting of the American Institute of Chemical Engineers (AIChE) on 17 November 2020. If you’d like to know more, the summary and the presentation material *1 can be found on the AIChE website, here .
References
*1 Daisuke Yagi, Hidenori Takai, Hiroki Watanabe. “The Algorithm to Discriminate Factors of Defects and Determine the Countermeasures from Process Data and Application to Highly-Functional Film Process,” presented at the 2020 AIChE Annual Meeting.