In this a project that required bridge building between Japan and the UK, how did Hitachi's collaborative creation support the development process? To obtain further insight on this process, we interviewed Yuichiro Kota, Senior Designer, Takashi Yoshizawa, Researcher, and Masataka Hidai, Researcher, all of the Research & Development Group of Hitachi, Ltd.
Unique pathways that all led to the railway business
KOTA: I am currently a Senior Designer in the Product Design Department, Global Center for Social Innovation – Tokyo. Ever since joining the company I have worked as a product designer. I attended an art university where I studied industrial design. While I conducted research on automobile design during my days as a student, I thought I would search for a field where I could thrive once I began thinking of my career. Automobiles are expensive, however the design adopted for them is somewhat uniform. I thought that there was room for growth in the design of household appliances, so I decided to pursue a career in household appliance design. I looked for a way to become a household appliance designer and joined Hitachi.
Upon joining Hitachi, I was in charge of cellular phone design. In fact, I have been involved in almost all of Hitachi's cellular phones such as stick type, foldable, sliding, and dual-axis rotation, can say covering all of Hitachi's cell phone design history. While the cell phone business was still steady, I shifted to the railway business. Designers in the railway business have multiple responsibilities including rolling stock design, passenger information systems, and station facilities. For rolling stock design, we cooperate with partners inside and outside the company to meet varieties of the user's requirements.
HIDAI: I am a researcher in the Advanced Simulation Research Department, Center for Technology Innovation – Mechanical Engineering. During my school days, I worked in a control theory laboratory and researched how to mathematically describe objects that were to be controlled, how to move them, and how to stop them. I always liked mathematics more than physics, and when I was being assigned to the laboratory, I wanted to pursue control theory because I thought it was an interesting idea when I came across it in class. When I was assigned to the laboratory, my professor said, "You can choose what you want to control in your research on your own." Because I liked railways, I decided to mathematically model railway rolling stock control. I was able to read academic articles to model the railway rolling stock and was able to receive instructions on control theory at the laboratory. Eventually, I enrolled in a master's course to continue my research.
As I had conducted this type of research for some time, there was a natural desire within me to work in the railway industry. Upon considering railway companies, manufacturers, and research laboratories, I thought Hitachi was compatible and they ended up hiring me. Even after joining the company, I have had the opportunity to conduct desk study research in conformity with theoretical formulas on matters such as derailment-resistant railway rolling stock safety and shaking when in motion. In reality, rolling stock do not always behave in ways predicted by equations, and this makes my work difficult. However, I believe that the steadiness of the work goes well with my personality.
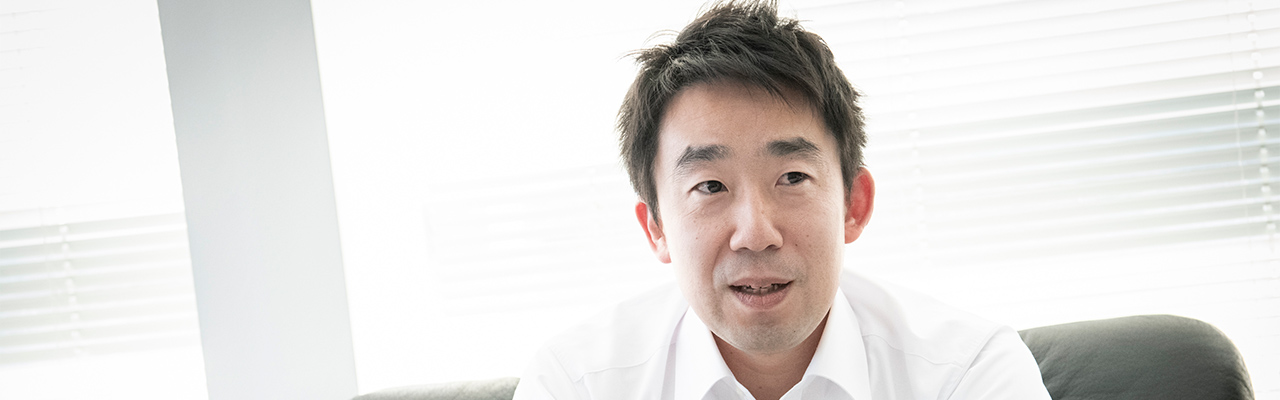
YOSHIZAWA: I am a researcher in the Reliability Science Research Department, Center for Technology Innovation – Mechanical Engineering. In my university days, I conducted research on medical robots. We made remotely operable devices to conduct surgical experiments. While surgical robots are now in use, when we were conducting research, we felt that this technology would not be applied for quite some time. When I started working for Hitachi, my desire was to conduct research on Hitachi's medical robots, but I was assigned to research related to automobiles. Hitachi creates components that reduce the noise and vibrations of automobiles, and I was engaged in researching this. I was even temporarily relocated to the U.S., and upon returning to Japan I have been researching how to reduce the noise and vibrations of railways. The technological fundamentals of noise and vibrations are similar for both automobiles and railways.
Aiming to secure long-term profits with overseas businesses
KOTA: I would like to briefly explain how we got the contract from the UK's IEP. In a situation where we could not anticipate Japan's railways business market to grow, Hitachi had a reason to expand its business overseas. When we looked at the overseas market, the UK was a relatively stable market. In addition, there were no UK original rolling stock manufacturers in the UK, and there were quality and delivery issues that emerged among rolling stock manufacturers in Europe. Moreover, large-scale investments in railway businesses by the UK government were anticipated after 2000, and there were even opportunities to take on the operations of maintenance services. Therefore, Hitachi targeted the UK as a market for business growth as it had the potential to secure long-term profits.
At first, we tried a few bids, but could not win a contract. Upon analyzing the reasons, we found that in Europe, Hitachi is seen as a manufacturer of household appliances. We were asked many questions such as, why railways? Why are you trying to come to the UK? Can you really start a business that grows roots in the UK? And, can you provide Japanese quality in the UK? Under these circumstances, we increased the number of exhibitions, seminars, lectures, and proved the performance and functions of Hitachi's technology with test trains that installed Hitachi's equipment on the UK's old rolling stock, in order to establish the Hitachi brand in the railway industry in Europe. Furthermore, Hitachi has since increased the number of local employees and has specifically demonstrated that Hitachi will commit to do rail business in the UK.
Thanks to these efforts, in 2005, Hitachi received an order for British Rail Class 395 high-speed rolling stock that was Hitachi's first order from Europe. The rolling stock, nicknamed Javelin, started operations in 2009. During the 2012 London Olympics, these trains were used as a shuttle service running between St. Pancras Station and the Olympic Park. Class 395 rolling stock strengthened Hitachi's railway business by demonstrating Japanese quality and on time delivery, such as the fact that the trains were ready for service six months ahead of schedule.
With improved presence and the accumulated track record, Hitachi's next target was IEP. Hitachi had already conducted thorough preparation. The IEP includes the delivery of 866 rolling stock, a 27.5-year maintenance agreement, and, according to a report at the time, it was a super large-scale contract worth 5.8 billion pounds or a 1 trillion yen. In short, the IEP would be a large business accomplishment if we could win the contract.
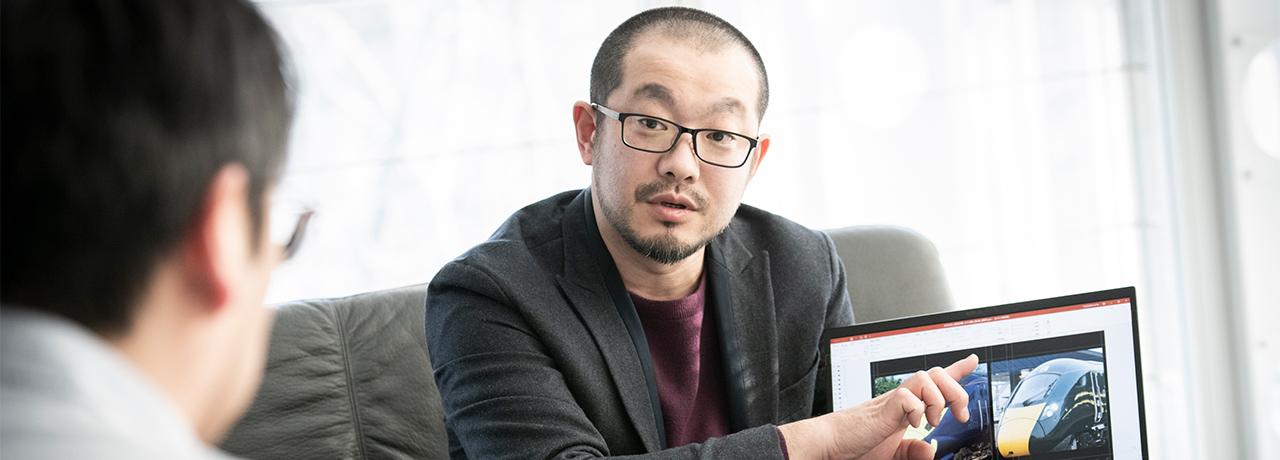
Bi-mode technology runs on both electrified and non-electrified sections
YOSHIZAWA: Although Hitachi was appointed as a preferred bidder in 2009, shortly afterwards, we were faced with complications due to the European sovereign debt crisis. However, in 2012, we signed the first contract covering Great Western Main Line (GWML) followed by the contract covering East Coast Main Line (ECML) in July 2014. Essentially, the IEP is a project that upgrades the old trains that has been towed by locomotives for 30 to 40 years. The GWML and the ECML, where the rolling stock will operate, have both electrified and non-electrified sections. From the get-go, one requirement was that the new rolling stock needed to be able to operate on both electrified and non-electrified sections.
With the impact of the European sovereign debt crisis, we were requested to increase the riding capacity and improve acceleration performance. Therefore, we proposed bi-mode trains which can generate energy within the train. In electrified sections, bi-mode train uses electric power collected from the overhead catenary to run the traction motor. On the other hand, in non-electrified sections, they generate electricity by activating the diesel generator unit installed underneath the floor of the generator units to power the motor. With this set up, the train can operate in both electrified and non-electrified sections. As the bi-mode train also provides sufficient acceleration performance, we were able to close the deal of the IEP. However, this means that a diesel engine must work below the seats of the passengers. In other words, passengers may feel that the engine is noisy if proper noise insulation measures are not taken. For this reason, we put effort into creating a device that would absorb both vibration and noise. However, there is no magical solution for noise and vibration prevention. Therefore, we carefully and properly executed the general method employed to reduce noise and vibrations.
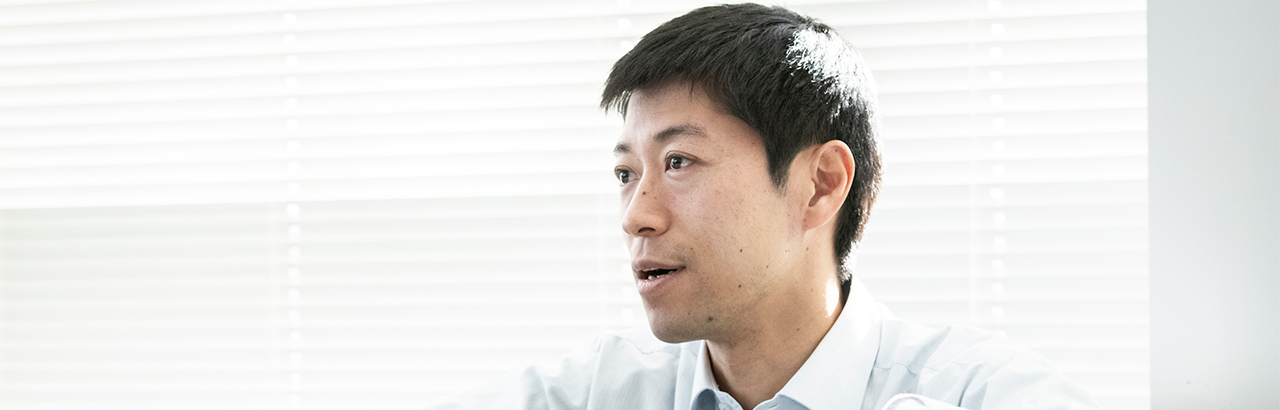
HIDAI: The success of Class 395 was a major factor for winning the IEP contract. In fact, it was during the delivery phase of Class 395 project that bidding for the IEP began. Setting up a factory in the UK and job creation in the local community also helped Hitachi to close the deal.
Thorough customization with Japan-UK cooperation
YOSHIZAWA: The IEP project had detailed specifications on many fronts. Hitachi trains are designed based on its design platform with customization to satisfy each customer's requirement.
Despite this, Hitachi took a Japanese way of approach. We listened to our client's requirements, and customized our products accordingly, with a thorough attention to detail. Hitachi7s proposal will be based on these very detailed studies. In fact, there are only a couple of bi-mode trains in the global market and neither Hitachi had an experience for this bi-mode design. However, we believed Hitachi's potential to develop this new product.
KOTA: We established Hitachi Rail Europe in the UK and worked on customizations and localization in partnership with Hitachi's laboratories and factories in Japan. After we won the bid, we created a full-sized mockup of the cab and the railway operators have touched it so that they could critique it, and also created a complete mockup of the first carriage to conduct some final checks. These kinds of physical operations cannot be completed remotely from Japan. While I went to the UK to help with the design, I saw the local team at Hitachi Rail Europe took the lead on the project. In short, I believe one reason we were able to conduct detailed customizations was because we localized operations by establishing Hitachi Rail Europe.
HIDAI: As we started manufacturing rolling stock, the railway operators made some comments on the loudness of noise during some test runs, which required various responses. However, the project also required much communication between the manufacturing that was done in the UK and the R&D which took place in Japan. One expert from my department was sent to the UK on a long-term basis and played the role of communicating demands from Hitachi Rail Europe to the units in Japan. I believe communications between the UK and Japan were smooth because there was a window person in the UK, which enabled us to communicate effectively with the teams in the UK.
KOTA: It was almost as if there was a small Japanese development unit in Hitachi Rail Europe. Detailed communications with Japan were conducted in Japanese, while local connections were established by Hitachi Rail Europe. This operational style was indispensable to the collaborative creation between Japan and the UK.
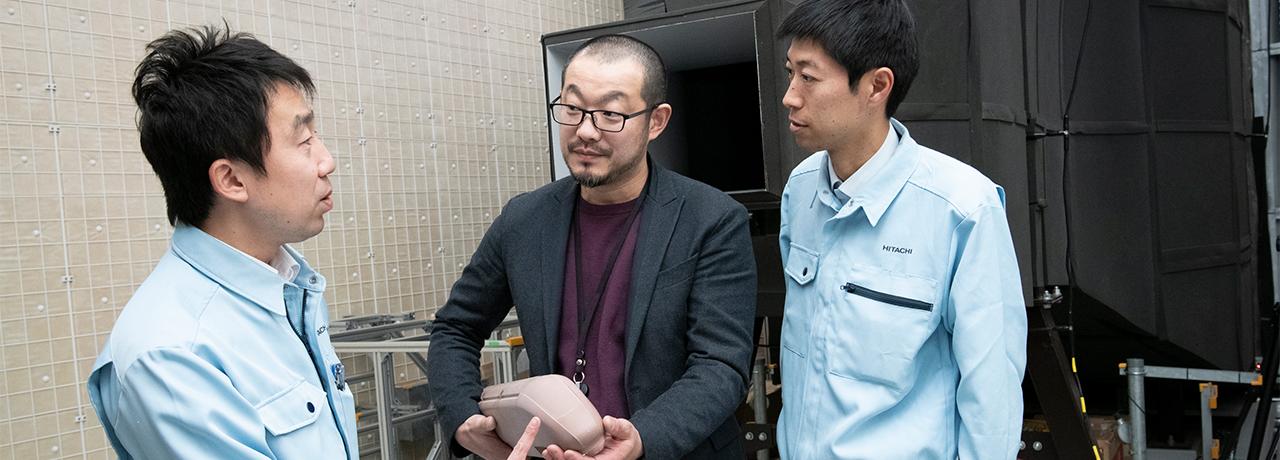
Supporting operation and maintenance with design
KOTA: As for the design aspect, there were parts of the Class 395 that were modified for the IEP. The leading vehicle for Class 395 has a flush surface design, which is an entirely flat surface that extends even to the windows and windshields. For this reason, the shape of the windshield is complex, which also makes it heavy and thick. For the IEP, however, strong character lines were used on both sides of the glass from the front end of the leading vehicle, and furthermore, the window and windshield portions were slightly indented compared to the exterior of the rolling stock. In fact, this design is also used for windshields of automobiles. With this, there was no need for the shape of the glass to be complex to make it fit with the curved exterior. The weight and thickness of the windows and windshields was limited to around two-thirds of the weight and thickness for Class 395 rolling stock, which also improved the productivity of the glass.
In addition, not only did this design solve problems encountered during the manufacturing stage, but it also brought about benefits to the operations and maintenance of the trains. This is because the indent between the glass and the exterior of the rolling stock made it easier to seal the glass. Indented glass can easily be sealed even in unfamiliar conditions, which improves maintenance when windows or windshields need to be changed.
YOSHIZAWA: There is an operation of regulation called "train availability" that is precisely set in the terms of the contract with the railway operators in the UK. This regulation sets detailed requirements such as the time during which rolling stock must be operable on a daily basis, or the time frame in which rolling stock must be replaced if there is an accident or failure. Because there are penalties if these requirements are not met, the ease of rolling stock operations and maintenance was important during development. It was under these circumstances that we were asked to develop rolling stock in partnership with the design department.
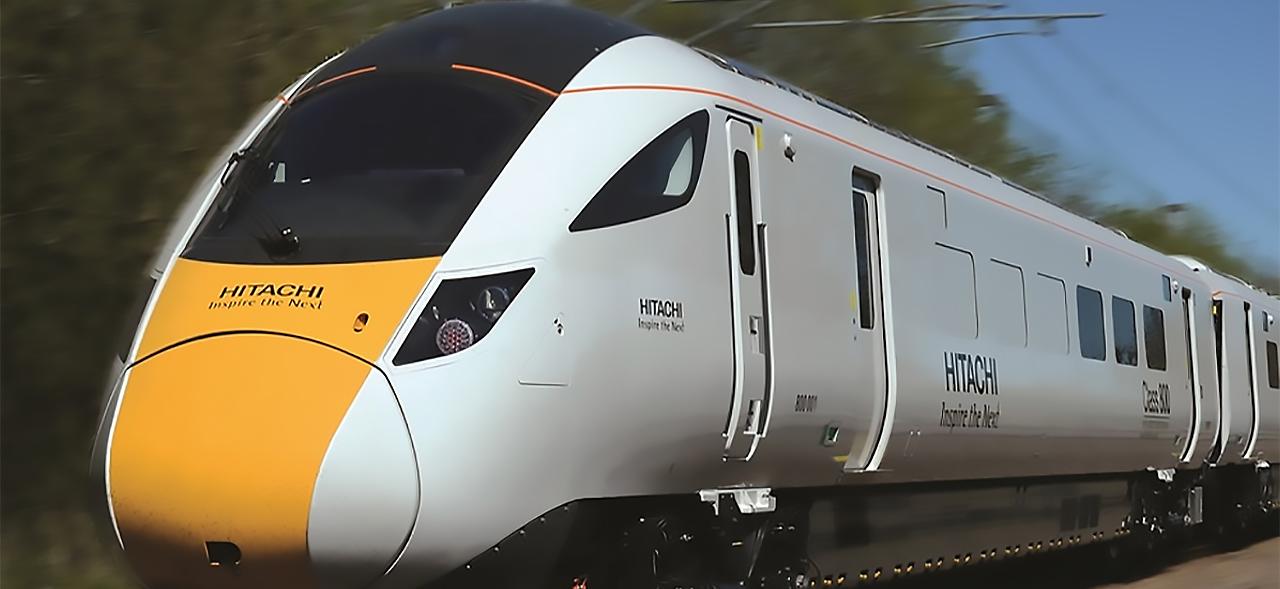
Enhanced awareness to collaborate beyond the realms of expertise
KOTA: Communication styles have also been changing between Japan and the UK. Nowadays, we can easily conduct video conferences while sharing virtual reality (VR) and computer-aided design (CAD) screens, but this was not possible just 5 years ago. We now think that it would be possible to collaborate with British designers if we combined video conferences with VR. In fact, if we were able to place a VR rolling stock in a shared space where we could draw on it, we would likely be able to communicate smoothly. While we had thought to implement VR around 2013, it was not a realistic option at the time because supercomputer processing was needed. However, high-functioning laptops would now enable us to conduct such operations.
HIDAI: Having been involved in railway technological development for around 10 years, I think it is important that we "break through barriers." In machinery technologies, various people conduct R&D in their fields of expertise. The reality is that even sound and vibrations are handled in different fields. However, from my experience communicating with people overseas, I have started to think that it is important to conduct research beyond one's own field of expertise. That is to say, I believe the strength of a general electronics manufacturer is that the rolling stock division and the power division can cooperate to create even better products. I feel as though I must keep saying this so that those involved in machinery can break through barriers and reach beyond their own fields of expertise.
YOSHIZAWA: When predicting vibration and noise, it is particularly difficult to predict how loud noises might be. While we are currently predicting a certain level of noise in the design stage, actual results are often different from forecasts. I am repeating nothing new when I say this, but with trains, there are multiple causes of noises such as the bogies, pantographs, and atmospheric noise. One of my goals is to perform design while being able to predict these composite noises with simulations.
HIDAI: Railway design has many parts that are not in line with theory. There is much value in knowledge that has been learned through experience. We must take away the barrier created between theory and experience to expand the areas where we can work on, even if it is little by little.
KOTA: As for the design aspect, we believe that we must incorporate more global perspectives. The IEP and Class 395 are both said to be "Japanese" from time to time. However, in the global market, various cultures and people who think differently utilize railways. Railways must be loved and must be used for a long time. When we think in this way, my desire is to hold a global perspective and design while incorporating some strengths of Japan. By knowing ourselves better and respecting the good parts of Japanese culture, I believe we can make designs that will be accepted in the global market.
Notification
- Publication: November 29, 2019
- Professional affiliation and official position are at the time of publication.
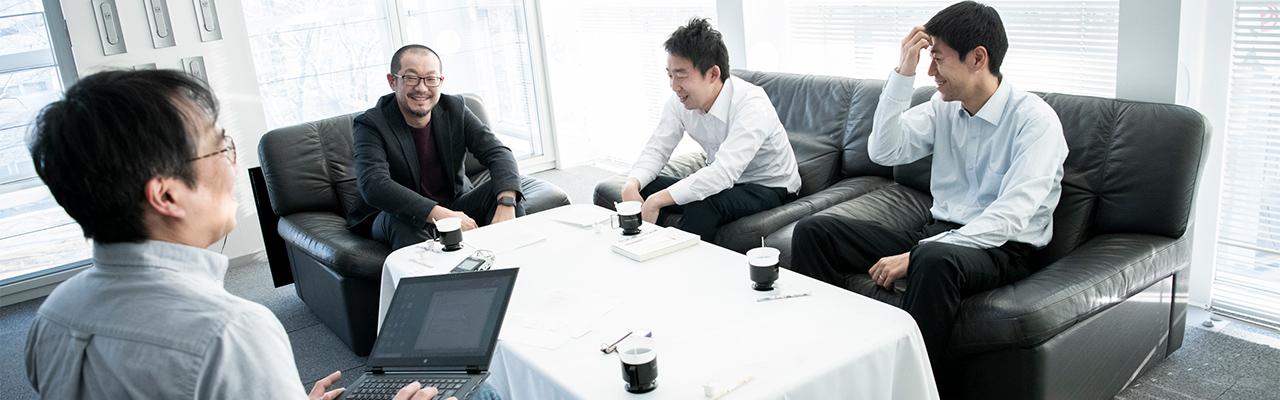