Hitachi has developed a radial-gap*1 amorphous motor realizing greatly improved efficiency and compactness, able to operate at higher rotational speeds than ordinary industrial motors, with the aim of saving energy in air compressors, fans, pumps, and other industrial utility equipment. To verify the effectiveness of this technology in utility equipment, a compact direct drive*2 air compressor (Figure 1) was developed and operation testing has begun. The aim will be to promote energy efficiency by applying this technology to various kinds of industrial equipment, helping to realize a carbon neutral society.
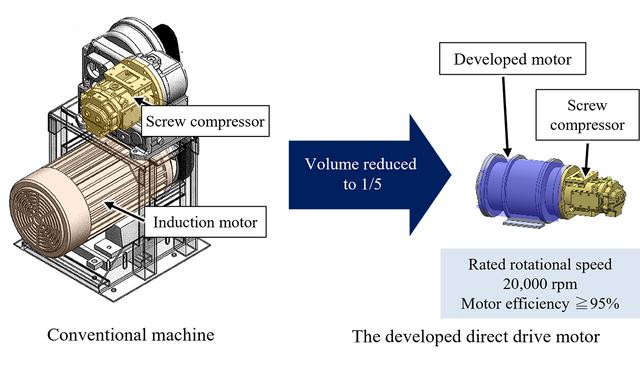
Figure 1: Internal structure of screw air compressor
Using low-loss amorphous metal*3 in the core, Hitachi developed an amorphous motor in 2008.*4 This was followed by the development of low-loss magnetic circuits, as well as axial support structures and cooling structures to reduce axial vibration and overheating from high rotation speeds. These advances drew on the motor design and production engineering know-how Hitachi has built up over the years. With the radial-gap amorphous motor (Figure 2), to enable use of low-loss amorphous metal, the core where energy loss tends to be concentrated was simplified by dividing it up, which realized both high motor speed and high efficiency, an elusive goal with conventional motor designs. As a result, at a rated rotational speed of 20,000 rpm,*5 the motor achieved efficiency of 95% or above (equivalent to IE5*6), at just 1/5 the size of a conventional motor. For this success, Hitachi won a NEDO Energy Conservation Technology Development Award*7 in 2024.
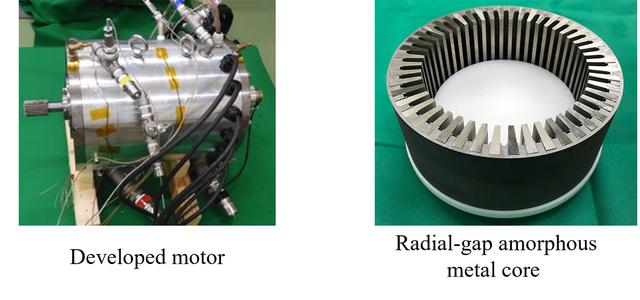
Figure 2: Appearance and core structure of the developed motor
To verify the effectiveness of these advances, a compact direct drive system was developed, incorporating this motor in an oil-free rotary screw air compressor, and operation testing has begun.
Working with customers, Hitachi plans to apply this technology to a wide range of industrial utility equipment including pumps, fans, and blowers, promoting energy efficiency and contributing to the realization of a carbon neutral society.
The results of the radial-gap amorphous motor development will be announced at the IEE-Japan (The Institute of Electrical Engineers of Japan) Industry Applications Society Conference,*8 held August 28-30, 2024.
Acknowledgement: Part of the research announced here was carried out under the New Energy and Industrial Technology Development Organization (NEDO) Program to Develop and Promote the Commercialization of Energy Conservation Technologies to Realize a Decarbonized Society / Development of a Super-efficient Utility Drive System.
*1 A motor design in which the airgap flux components all flow in the radial direction (perpendicular to the axis of rotation). The model is one example showing the difference in motor structure.
*2 A mechanism in which the motor drives a load directly without a transmission device.
*3 Here used to mean an amorphous metal consisting mainly of iron.
*4 “Amorphous Motor with IE5 Efficiency Class,” Hitachi Review Vol. 64 (2015), No. 8.
https://www.hitachihyoron.com/rev/pdf/2015/r2015_08_109.pdf
*5 Rated rotational speed is the rotational velocity that is output when the specified voltage and other conditions are applied, given as rotations per minute (rpm or r/min).
*6 The highest level in the international standards for energy efficiency of motors set by the International Electrotechnical Commission (IEC).
*7 Executive Director’s Prize received for "Development of a Super-efficient Utility Drive System".
https://www.nedo.go.jp/news/press/AA5_101722.html(in Japanese)
*8 2024 IEE-Japan Industry Applications Society Conference.
https://www.iee.jp/en-ias/annual-conference/
For more information, use the enquiry form below to contact the Research & Development Group, Hitachi, Ltd. Please make sure to include the title of the article.
https://www8.hitachi.co.jp/inquiry/hitachi-ltd/hqrd/news/en/form.jsp