Vibration reduction and 34% downsizing for high-speed EV motor of 100 kW and 22,000 rpm
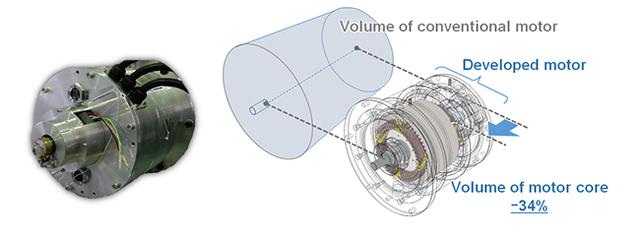
Fig 1. Volume comparison of developed compact high-output motor (100 kW, 22,000 rpm) and conventional motor.
Hitachi, Ltd. has developed a compact and high-power permanent magnet motor and its control technology, suitable for expanding the cruising range and the vehicle interior space of EVs. To achieve the compact and light-weight characteristics, we developed a new rotor*1 that can reduce its vibration under a rotation speed twice as fast as a conventional motor, along with a weldless coil for the stator*2. We also developed a carrier-shift control that can improve both vibration and energy loss under the high-speed rotating condition. We fabricated a high-power (100 kW) and high-speed (22,000 rpm) motor by using these technologies and achieved both a vibration reduction and 34% downsizing.
In the future, we will contribute to the creation of a decarbonized society by utilizing these next-generation technologies and in-wheel motors*3 for various EV powertrains*4.
Technology details
There are four key requirements for the powertrain systems of electrified vehicles such as EVs: (1) lighter body weight (for extending the cruising range), (2) downsized powertrain (for expanding the vehicle interior space), (3) low noise and low vibration, and (4) cost reduction. For motors with big volumes, the compact and high-power characteristics are particularly important. The downsizing approach that makes the motor speed higher and provides a large torque by reduction gears has grown popular in recent years. However, there are issues that vibration and energy loss tend to increase significantly under high-speed rotating conditions. Hitachi has developed a compact, low-vibration and loss-reduction technology by applying motor know-how, control technology, and fast magnetic field calculation tool, without decreasing the rotor strength and its torque under high-speed rotating conditions. The features of our developed technologies are as follows.
1. Vibration reduction and downsizing technologies for permanent magnet motor
We have developed a new rotor structure that reduces torque ripple, which causes vibrations, in order to reduce vibration under high-speed rotating conditions. Specifically, we provided an asymmetrical pair of grooves and extended flux barriers*5 in the vicinity of the rotor magnet. The torque ripple has been improved by optimizing the shape of the grooves and the flux barriers (Fig. 2 (1)). Additionally, we optimized the shape of the magnetic flux barrier for relaxing the stress concentration in the rotor core while maintaining the effective magnetic flux value generated from the magnets, and improved the rigidness to centrifugal force under high-speed rotating conditions (Fig. 2 (2)). These design technologies have reduced the vibration components of the torque ripple by around 50% from a low-speed region to a high-speed region (22,000 rpm), leading to a small enough vibration level that drivers feel is acceptable.
Hitachi has also developed a new assembly method for the flat wire coil that is wound around the stator in order to further downsize the motor. Conventionally, a constant length of the welding point at the coil-end*6 is needed for flat wire coil assembling. We have developed a new coil joint technique in which the flat wire coils are fitted with each other*7 around the center of the axial and verified it by drive tests (Fig. 3). The developed technologies can improve the axial length of the coil-end by 27% and the frame weight by 14%.
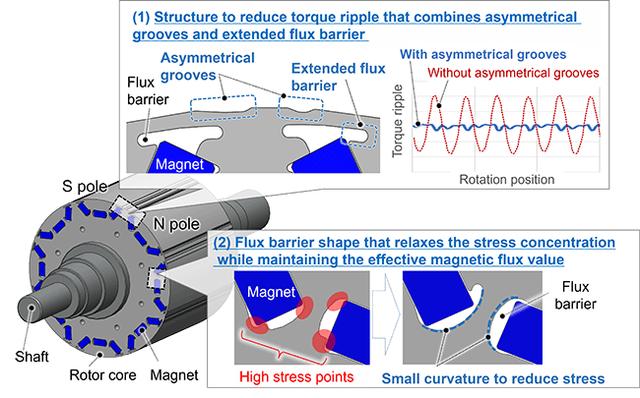
Fig 2. Rotor structure to reduce torque ripple and vibrations under high-speed rotating conditions.
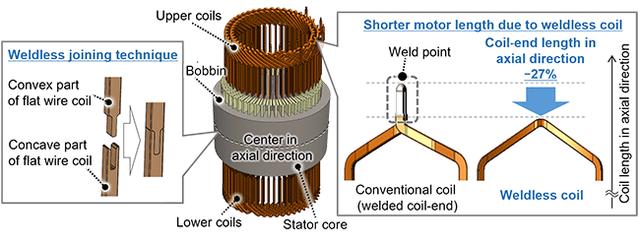
Fig 3. Technique to fit convex part of a coil and concave part of another coil, dispensing with the need for welding the coil-end.
2. Vibration-reduction and loss-reduction technologies (carrier shift control)
A high-speed motor operation generates AC copper loss in the coil, eddy current loss in the magnet, and iron loss in the stator and rotor cores. These energy loss issues prevent the extension of the EV range. Hitachi has developed carrier shift control technology that enables a reduction of both motor vibration and energy loss. First, by shifting the phase of the carrier wave*8 for a PWM*9 pulse against the voltage command of the motor control, the torque ripple under high-speed rotating conditions is reduced and the motor vibration is suppressed. Second, we added a new shift pattern to the carrier shift control, which can reduce the harmonics that cause energy loss. This control technology can improve the energy loss of the coil and the magnet by 28% compared to the conventional technology (Fig. 4).
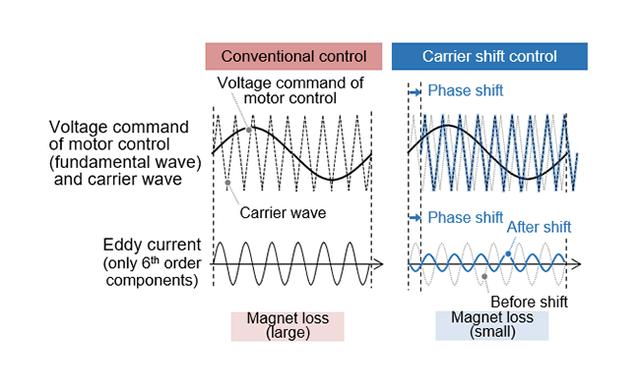
Fig 4. Carrier shift control technology that reduces motor vibration and energy loss under high-speed rotating conditions.
After applying our technologies to the motor and investigating the effect on downsizing and vibration reduction, we confirmed it can reduce the volume of the motor core by 34% with an improvement in the vibration under conditions of high power (100 kW) and high speed (22,000 rpm). Furthermore, the power density*10 of the compact and high-output motor has reached 4 kW/kg, which is twice higher than the Hitachi's conventional geared motor.
*1 Rotor: A rotating part of a motor, in which magnets are embedded.
*2 Stator: A fixed part of a motor, which is equipped with coils to allow current flow.
*3 In-wheel motor: A motor fitted inside a vehicle wheel.
https://rd.hitachi.com/_ct/17701584
*4 Powertrain: A piece of equipment that is the source of a vehicle's motive force, or that conveys motive force to the vehicle wheels.
*5 Flux barrier: A pocket of air that prevents flux.
*6 Coil-end: The portion of coils that extrude from the stator core in the axial direction.
*7 Flat wire coils fitted to each other: Fitting the convex part of a coil to the concave part of another coil.
*8 Carrier wave: A comparative signal that converts a voltage command of motor control to pulse width.
*9 PWM: Pulse Width Modulation. A method of controlling the amount of energy supplied to a motor with pulse width.
*10 Power density: The ratio of output power to weight relating to the motor. The weight includes the motor frame and the motor shaft.
For more information, use the enquiry form below to contact the Research & Development Group, Hitachi, Ltd. Please make sure to include the title of the article.
https://www8.hitachi.co.jp/inquiry/hitachi-ltd/hqrd/news/en/form.jsp