Visualizes tacit knowledge of human skills, improves on-site productivity, and supports skill transfer
Aiming to improve on-site productivity and deal with a shortage of human resources due to the generational turnover of skilled welders, Hitachi, Ltd. has developed automation technologies for digitalizing the advanced know-how of skilled welders and equipping robots with that know-how. These technologies enable the automation of complex welding work by visualizing the tacit knowledge possessed by skilled welders and converting that knowledge into high-precision robot operations. Filling in a gap between two members to be butt welded together is one example of a complex welding task that up to now has been considered difficult to automate (Fig. 1). On constructing a prototype of a welding robot and using it to perform welding work, we confirmed that it could weld with nearly the same quality as a skilled welder. Going forward, Hitachi plans to conduct verification experiments using these technologies and to promote further technology development in collaboration with its customers. It also seeks to contribute to greater productivity at manufacturing sites and to the transfer of skills possessed by experienced welders.
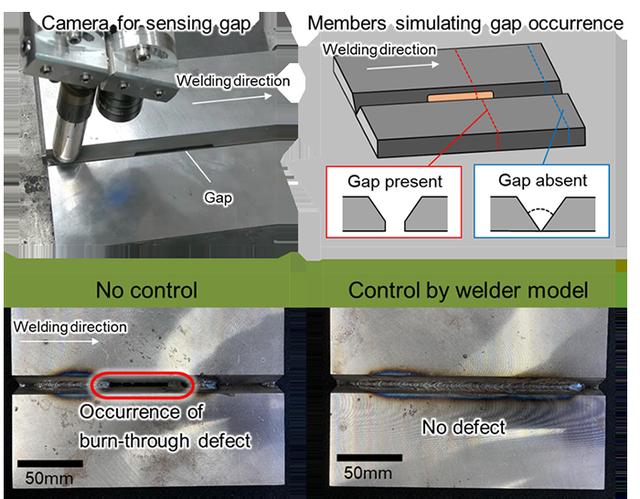
Fig. 1 Automation by digitalizing know-how of skilled welders
Background and issues
- Amid concerns about the loss of high-quality manufacturing power cultivated over many years owing to the generational turnover of skilled welders, there is a need for some type of mechanism for efficiently passing on the tacit knowledge of welding skills.
- The automation of advanced, complex welding work is slow to take form, so there is a need for technical innovations that can improve both quality and productivity.
Developed technologies
- Technology for measuring and visualizing welding skills with high precision
- Technology for converting welding actions to a model required for robot control
- Machine learning algorithm for detecting changes in the welding state with high precision
- Technology for autonomously controlling the best operation according to change in the welding state
Verified effects
- We constructed a prototype of a welding robot equipped with a camera for sensing changes in the welding state and incorporating the operations of a skilled welder in the form of a model. Then, on using the robot to perform welding work simulating the occurrence of a gap between two members to be butt-welded together—a situation that requires a high level of skill to deal with—we verified that welding could be performed with nearly the same quality as a skilled welder.
Published papers, conferences, events, etc.
- Hitachi plans to present a portion of this technology development at the 2021 Spring Meeting of the Japan Welding Society.
Details of developed technology
1. Technology for measuring and visualizing welding skills with high precision
The movement of the torch*1 in welding operations is an important element of quality control in welding along with other welding conditions. The analysis of torch operation has been analyzed in the past using camera images, but the strong emission of light during arc*2 generation in welding has made it difficult to perform high-precision measurements. This problem generated a need for a new technique that could sense welding operations with high precision. We therefore developed technology for using multiple cameras and motion-capture schemes to sense a variety of conditions such as the welder’s gaze and the position, height, and velocity of torch movement as well as the state of the weld zone. We also developed technology for quantifying this welding work and visualizing the quantified data. These technologies have made it possible to make high-precision measurements with a resolution on the order of approximately ±0.1 mm compared with that on the mm order in conventional image analysis.
2. Technology for converting welding work to a model required for robot control
Incorporating precisely measured welder movements in robot control requires that they be converted to a model applicable to control. We therefore measured the actions taken by a welder to adapt to changes in the welding state and modeled those movements. For example, a gap can easily occur between two members to be welded (butting faces) due to errors in member dimensions or deformation caused by welding. This gap is a major factor affecting welding quality, so the welder will move the torch in unique ways in step with gap fluctuations to suppress the occurrence of defects. By therefore measuring the adaptive actions of the welder against a test sample simulating such a gap, we constructed a model of robot control conditions that could deal with gap fluctuations.
3. Machine learning algorithm for detecting changes in the welding state with high precision
The welder visually detects a gap in a welding groove and controls the movement of the welding arc according to that change. To achieve such an advanced movement in a robot, this gap in the groove has to be detected with high precision and robot control has to adapt to that fluctuation. To this end, we developed technology that uses a deep-learning image-processing technique to directly measure information near the weld zone even in an arc-generating environment.
Specifically, we developed an image-processing algorithm that recognizes and removes spatter*3, a factor in measurement error, and used a deep-learning model. This made it possible to achieve robust measurements of information near the weld zone.
4. Technology for autonomously controlling the best operation according to change in the welding state
We developed welding technology featuring feed-forward control that can synchronize the control of welding operations and welding-machine output by linking a PC*4, PLC*5, welding machine, and robot via socket communications and managing that information in an integrated manner.
Using the above elemental technologies, Hitachi has completed a basic study on automation that reproduces the operations of a skilled welder through the autonomous control of a robot.
*1 Torch: Heating instrument for melting and binding metal.
*2 Arc: An arc of light created by an electric discharge between two electrodes; welding that uses such an arc is called arc welding.
*3 Spatter: Melted metal that scatters from the weld pool due to an arc or other heat source.
*4 PC: Personal computer
*5 PLC: Programmable logic controller. Used for monitoring and control of industrial equipment and devices.
For more information, use the enquiry form below to contact the Research & Development Group, Hitachi, Ltd. Please make sure to include the title of the article.
https://www8.hitachi.co.jp/inquiry/hitachi-ltd/hqrd/news/en/form.jsp