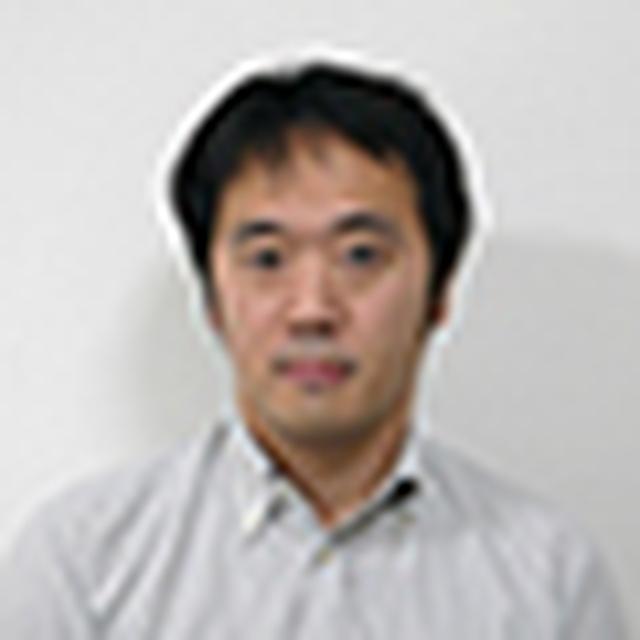
Yasutaka Serizawa
R&D Division, Hitachi America, Ltd.
Industrial IoT, the extension of the Internet of Things (IoT) in industrial sectors, and AI are increasingly seen as promising technologies to address multiple issues especially in the manufacturing sector, such as unscheduled downtimes which are a common occurrence and a major cause of lost productivity and delayed customer deliveries. While most of manufacturers identify it as a major issue, they lack the awareness and necessary tools *1*2 to resolve this problem. Industrial IoT and AI can provide effective solutions to both these problems. There are however challenges owing to the brownfield nature of industrial IoT where a typical deployment suffers inadequate data acquisition, ad-hoc data modeling, lack of data cleansing etc. This is further compounded when dealing with high-speed high-volume sensor data such as vibration, acoustic, ultrasonic etc. Therefore there is a need for a unified IoT system that’s AI-centric, i.e. creating a modular and scalable data pipeline that can realize an AI marketplace with plug-and-play orchestration of multiple analytics solutions.
Against this backdrop, our research explored an analytics-centric sensing system which supports real-time streaming data processing as well as scalable one-stop data configuration with feedback from analytics side. Figure 1 (left) shows our proposed conceptual system architecture. The streaming data generated from sensors is consumed by pre-processing function modules in signal processing part, and then transferred to analytics function modules in real-time streaming manner. The sensing system has an unified way to handle all the data sources, which requires an adaptation layer in the data acquisition part to extract different sensors and provide APIs (an application programming interface that allows software to access functions provided by other software) to the analytics part.
The other important aspect for the sensing system is an one-stop configuration for all the sensing or data processing parameters (e.g. sampling frequency, streaming size, bit width, filter types) based on input from the analytics side, as AI models require different data inputs depending on applications. Figure 1 (right) shows overall description of an implementation for acoustic sensors. In Figure 2, an example of the acoustic sensing system which has been implemented is shown along with various IoT-related function blocks. We utilized gRPC *3 to reduce message size and support scalability. The features of gRPC are characterized by serialization of data using protocol buffers and fixed data structure definable from system. In our implementation of the acoustic streaming data processing system, protocol buffer provides the analytics part with APIs for data acquisition and data processing part, which makes this system “analytics-centric”. In the gRPC-based communication of the proposed sensing system, the server and client are deployed on each part. A client's request in analytics part includes the configuration information such as parameters for the streaming data, which is exchanged with gRPC servers deployed in lower-layer part. This architecture enables detailed configuration of each functional module and fine control of the data streaming pipelines. Owing to this broker functionality on the signal processing part and data acquisition part, the AI models can retrieve suitable data for input from different data sources.
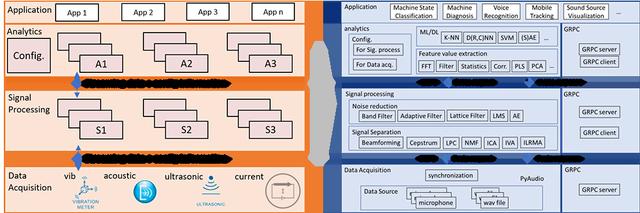
Figure 1: Proposed system architecture (left), and its implementation on acoustic sensing system (right)
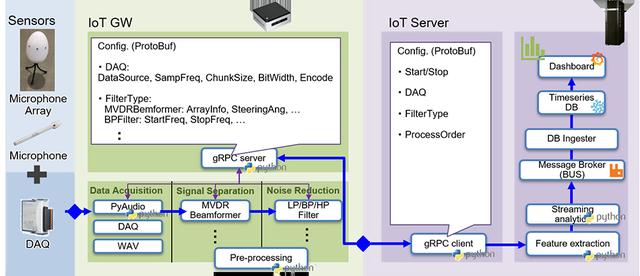
Figure 2: A simple example implementation of recommended acoustic sensing system
To verify this conceptual system architecture, we established two applications with acoustic-based AI: machine state classification and anomaly detection. The successful operation of both applications on the same system suggests that the developed system would reduce cost and the barrier to introducing an AI-based IoT system significantly.
In summary, we have developed a streaming sensor data processing system for AI-based industrial IoT which enables analytics-centric sensing configuration. This work will reduce cost and help remove the barrier of AI-based IoT system adoption for industry. For further details of our work we refer to the original paper available at https://www.sensorsportal.com/HTML/DIGEST/P_3134.htm.
Acknowledgements
Thanks to my co-author Yusuke Shomura with whom this research work was jointly executed, and my colleagues, Sudhanshu Gaur and Joydeep Acharya, for discussion on research direction as well as refinement of this blog.
References
*1 Salonen A., Tabikh M. (2016) Downtime Costing—Attitudes in Swedish Manufacturing Industry. In: Koskinen K. et al. (eds) Proceedings of the 10th World Congress on Engineering Asset Management (WCEAM 2015). Lecture Notes in Mechanical Engineering. Springer, Cham
*2 Radosław Wolniak, Downtime in the Automotive Industry Production Process – Cause Analysis, in Quality Innovation Prosperity / Kvalita Inovacia Prosperita 23/2 – 2019
*3 gRPC/Proto buffer, https://grpc.io/about/