Eliminating Manual Adjustments During Layout Changes of Automated Lines Through Mutual Recognition and Coordination Between Material Handling Devices
Hitachi has developed system control technologies that reduce on-site manual labor when establishing or changing the layout of goods sorting lines at warehouses and other logistics facilities. These new technologies automate the motion control program settings of each device while eliminating precise adjustments to the placement of the conveyors, automated guided vehicles, manipulators, and other material handling devices configuring the automated lines.
These new technologies also autonomously adapt material handling by identifying the position of other equipment using sensors, such as cameras mounted on each material handling device. The integrated controller for the whole automated line can identify the entire layout to set the motion control program of each material handling device according to the relative position and ID data between devices connected to the automated line.
The effectiveness of these technologies has been demonstrated using simulations which show the potential to reduce the time required for layout changes of a typical goods sorting line from four days to less than one day. In the future, Hitachi will deploy this technology to actual material handling lines to prove its value and encourage rapid practical implementation.
Hitachi developed these system control technologies as part of its autonomous and collaborative robotics technology platform*1, and announced some of its success at The Robotics and Mechatronics Conference 2021 (ROBOMECH 2021)
held by The Japan Society of Mechanical Engineers online from June 6 to June 8, 2021.
Technology details
Warehouses in the logistics field have rapidly increased the quantity and variety of products they handle with the expansion of mail-order markets driven by the spread of the novel coronavirus infection, which has also created even harsher warehouse work environments compounded by even greater labor shortages. These issues have heightened hopes for warehouse automation technologies. The mission of future automation systems is the aim to quickly and flexibly change layouts of automated lines according to fluctuating demand. Generally, warehouses and other logistics facilities struggle with the necessity for specialized technical adjustments and long-term automated line stoppages when changing layouts, including precise adjustments to the relative position of each material handling device as well as the configuration of the settings for programs to control the motion of these devices and manipulators.
Hitachi developed these system control technologies with the goal of eliminating manual adjustment work and reducing the length of line stoppages when changing layouts of material handling lines. This system control enables mutual adjustments of material handling devices making up the automated line as well as autonomous settings of the respective motion control programs. These system control technologies provide the features below.
1. Technology for mutual adjustments of material handling operations
Manual labor to precisely adjust the position and orientation of material handling devices configuring an automated line has been required to smoothly sort goods on conventional material handling lines. Manual work requiring specialized technical skills have also been essential for scribing and marking floors, finely adjusting the position between material handling devices, and making other relative positional adjustments.
Taking a new approach to overcome these challenges, Hitachi developed a technology that enables automated guided vehicles and manipulators to identify errors in the relative position between other material handling devices as well as the misalignments in the position and orientation of materials caused by those errors. This technology uses the data that is aggregated to mutually adjust the layout and handling operations of the material handling devices. Automated guided vehicles in particular use range finders to identify placement errors in material handling lines as well as confirm conveyor markers (two-dimensional IDs) to stop in the right place by precisely identifying the position to receive goods. Manipulators also prevent any collisions with materials (trays) during the sorting process by identifying misalignments in the position and orientation of trays carried by conveyors and automated guided vehicles using markers. These innovations enable smooth sorting of goods, even if the conveyors are misaligned.
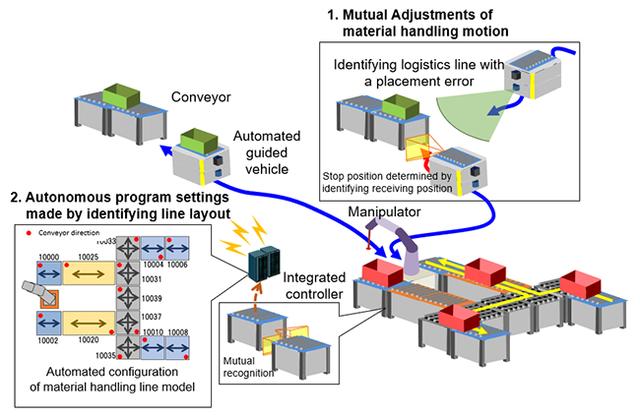
Fig 1. Mutual adjustments of material handling devices and automated settings of motion control programs via an integrated controller
2. Technology to automate motion control program settings by identifying the entire layout of the automated line
An expert engineer typically sets the program that controls the motion of each material handling device based on the layout of the entire material handling line. Therefore, this process also requires an engineer to specify the control program settings again for every layout change of the automated line, which is one reason that layout changes of material handling lines take so much time.
Hitachi developed this technology to automate the program settings that control the motion of each material handling device. This allows each of these devices to identify other adjacent material handling devices using markers while the integrated controller aggregates that data to grasp the entire layout of the automated line*2. Especially when a line is divided, the automated guided vehicle first autonomously creates a schematic diagram of the work zone using a range finder to correlate the layout before the change to identify the new divided line. Next, the automated guided vehicle loads the markers after the layout change to the material handling line in order to confirm the whole layout and automatically set travel routes to connect the divided lines.
Hitachi demonstrated the benefits of this technology using a simulation of an automated sorting line at a logistics warehouse*3. Even with errors in the orientation and placement of conveyors up to 17 degrees and 20 cm respectively due to a layout change to the automated line, the manipulator and automated guided vehicle autonomously adapted their movements (Fig. 3). The simulation also verified that the control system was able to reconfigure the control program for the handling operations in less than 10 minutes after a layout change to a line consisting of ten conveyors, one automated guided vehicle, and one manipulator. According to these results, this technology is expected to reduce the time required to change the layout of automated lines from the four days it usually takes to less than one day (Fig. 4). The tolerance of conveyor placement errors was particularly impactful in eliminating the manual labor necessary for scribbling and marking the floor, which should cut the time required for setting up conveyors in half. Moreover, automation of the manual settings done for the motion control programs of each material handling device enables automated lines to start up immediately after a layout change.
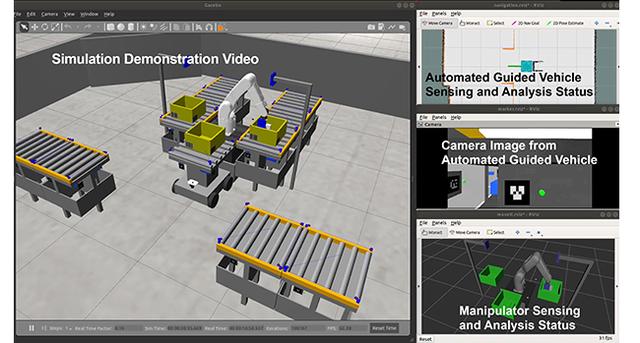
Fig 2. Simulation proving the technologies can properly handle materials even with conveyor placement errors by linking manipulators and automated guided vehicles
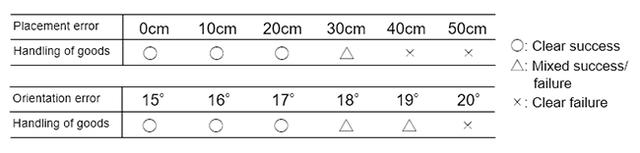
Fig 3. Confirmation of success in handling of goods in spite of conveyor errors
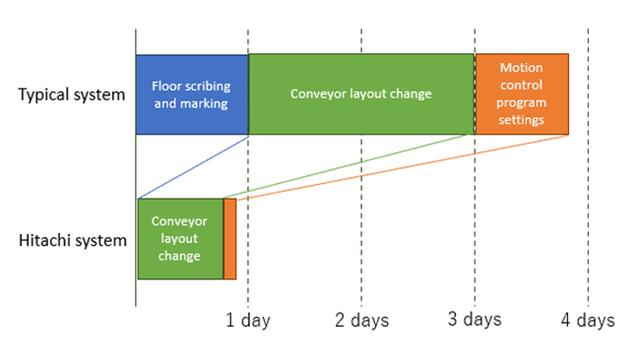
Fig 4. Impact analysis of on-site labor related to automated line layout changes
*1 Development of Autonomous and Collaborative Robotics Technologies for Advanced Automation (Hitachi Review) https://www.hitachi.com/rev/archive/2019/r2019_04/04b05/index.html
*2 N. Kimura et al., “Material Handling Modules Which Recognize Each Other for Cost Reduction of Changing Transportation Line Layout,” The Japan society of Mechanical Engineers Robotics and Mechatronics Conference 2021, June 2021
*3 The manipulator used in the simulation is modeled after the Denso VS-087
For more information, use the enquiry form below to contact the Research & Development Group, Hitachi, Ltd. Please make sure to include the title of the article.
https://www8.hitachi.co.jp/inquiry/hitachi-ltd/hqrd/news/en/form.jsp